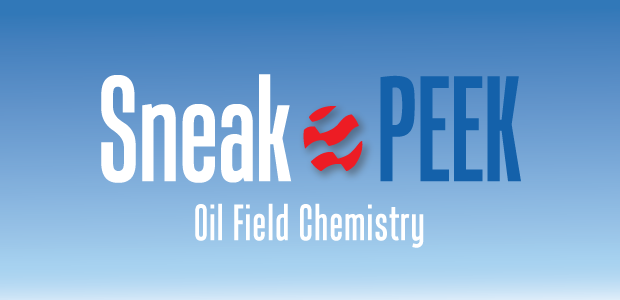
Powerful Chemistries Pair Attractive Returns With Environmental Gains
By Colter Cookson
According to a survey by Ipsos, only 22% of the world’s population considers the oil and gas industry trustworthy. Although oil and gas ranks above the government and traditional media, the low rating still may frustrate workers who see the steps the industry takes every day to improve safety, protect the environment and support local communities.
For context, even the technology sector, which garnered the most trustworthy rating, received that designation from only 34% of respondents. Despite intense media scrutiny and concerns about climate change, the report indicates the global public is “more likely to be neutral towards oil and gas companies than have an opinion about the sector’s trustworthiness; 22% find sector brands trustworthy and 34% untrustworthy, but (44%) sit somewhere in the middle.”
Noting that the industry’s ratings for all trust drivers improved between 2018 and 2021, Ipsos says that pool of undecided people may move to “trustworthy” if the industry continues to exceed expectations.
In a world where the phrase “environment, social and governance” has become ubiquitous, the industry has more opportunities than ever to highlight its good deeds. Today, those good deeds–which often provide both economic and environmental benefits–range from chemical program tweaks to intense research to expand produced water recycling and help conserve freshwater in arid regions.
“Environmental performance has become a more common topic of discussion among the stakeholders we represent,” says Kevin Duncan, vice president of operations for U.S. Energy Development Corp. “They want to put capital in companies that are mindful of the environment, so we make a point to emphasize that we have an ISO-certified environmental management system.”
While it is committed to stewardship and sustainability, Duncan stresses that U.S. Energy’s primary goal is to generate returns for its stakeholders. He notes that the company is relatively small, with 50 wells in South Texas, several Wolfcamp horizontals, eight Mississippi Lime horizontals and various stripper wells scattered across New Mexico.
“At our size, we have to be cautious about trying new technologies,” he reflects. “We cannot afford to make mistakes that would be costly for our stakeholders, so instead of experimenting, we look for technologies we know will be successful and economic, as well as ESG friendly.
To reduce diesel consumption, U.S. Energy Development Corp. employs a diesel catalyst on all its drilling and completion operations. According to the company, the catalyst shrinks fuel costs and emissions by cutting diesel use an average of 8%.
“One of our most exciting successes is a diesel fuel catalyst from Crown CRT that helps engines run more efficiently,” he comments. “On average, it cuts fuel consumption 8%. With diesel costing $4-$5 a gallon, the savings add up quickly.”
Duncan says U.S. Energy has used the catalyst on its drilling and completion operations since 2020. “The rig contractors and completion crews like the catalyst because it keeps engines clean and reduces maintenance costs,” he says. “It also cuts emissions of particulate matter by 50%, carbon monoxide by 30%, nitrous oxide by 8% and volatile organic compounds by 50% while reducing overall carbon dioxide emissions about 8%.”
Safer Chemicals
When pandemic-induced supply chain issues made traditional oil field chemicals more expensive and harder to find, U.S. Energy partnered with a South Texas chemical provider to find solutions. “They came up with several ideas we thought would improve economics while providing ESG benefits,” Duncan relates. “For example, they suggested switching many of our wells from water-soluble corrosion inhibitors to oil-soluble corrosion inhibitors.
“Water-soluble inhibitors can cause emulsions in produced water that have to be dealt with before disposal,” Duncan explains. “In contrast, the oil soluble inhibitors can be left in the oil that gets sent to the refinery.”
For remediating scale, U.S. Energy has moved from hydrochloric acid to ascetic acid, Duncan continues. “Ascetic acid gets the job done but comes with fewer environmental and safety risks,” he explains. “We still take the same precautions we would with hydrochloric acid, but if we do have a leak or other unexpected event, the damage will be less severe.”
Water Recycling
Using produced water as the base for completion fluids can have tremendous benefits, says Coby Reynolds, director of water treatment for SwiftWater, a TETRA Technologies company operating in West Texas. “At scale, recycling produced water is less expensive than injecting it into a saltwater disposal well,” he reports. “We can build a facility capable of processing 120,000 barrels of water a day for a fraction of the cost required to permit and drill a disposal well.”
Large water recycling facilities can have extremely low operating costs, Reynolds adds. “In some areas under certain conditions, we can treat water for less than $0.15/bbl,” he says. “The exact cost will vary based on the volumes and targeted water quality, but even a facility that only processes 30,000 bbl/d can have the economies of scale to make recycling economic.”
Low recycling costs have hardly sprung up overnight, Reynolds notes. “Ten years ago, the cost to treat each barrel of water often fell between $0.40 and $0.70, and we thought most facilities would only handle 5,000 bbl/d,” he recounts. “Today, we see recycling systems with centralized facilities that process 100,000-150,000 bbl/d.
“As the demand for water recycling has grown, manufacturers have responded by developing new technologies and researching ways to optimize the water recycling process,” he comments. “Instead of repurposing treatment systems from other industries, we now deploy highly automated, purpose-built equipment.”
Thanks to automation, a single technician can manage a facility that cleans 120,000 bbl/d, Reynolds says. “The automation systems take care of routine optimizations such as adjusting how much chemical is applied based on oxidation reduction potential, pH and flow rate,” he says. “The technician still needs to make changes, but those can be as simple as plugging a hose into a new chemical tote and telling the PLC the new chemical’s concentration.”
Robust automation has made water treatment facilities extremely efficient and cut the cost of reusing produced water in completions, TETRA Technologies reports. The company says a single person can manage a facility capable of treating 120,000 barrels of produced water a day.
Expanding Access
Water recycling’s strong economic and environmental benefits are prompting service companies to give more operators a chance to take advantage of it, Reynolds reports. For example, midstream companies are building pipelines to move produced water to areas with significant completion activity. Reynolds points out that these companies are consolidating to shrink their operating costs.
But reuse in completions will not entirely absorb produced water volumes. In a September report, the Texas Produced Water Consortium says, “even if operators were able to utilize treated produced water for 100% of their production activities in the Permian Basin, there would still be millions of barrels of excess produced water generated every day, needing to be disposed or otherwise managed.”
The Texas Produced Water Consortium and the New Mexico Produced Water Research Consortium are among several organizations investigating ways to use produced water outside the oil and gas industry, Reynolds notes. “Texas and New Mexico are arid states. If we can reduce produced water’s total suspended solids to a point where it’s safe to water cotton and other nonconsumable crops, we can help preserve freshwater supplies and give nearby communities even more reason to support oil and gas development,” he reflects.
Produced water has been treated and reused or discharged in California, Colorado, Oklahoma, Pennsylvania and Wyoming. Reynolds says one key to replicating and expanding those projects in the Permian will be cost-effective treatments. “We are going to see some exciting technologies come out to help the industry treat water more efficiently,” he predicts. “At TETRA, we have partnered with two desalination experts–KMX and Hyrec–to bring their technologies into oil and gas. Both have a ton of promise.”
The desalination processes produce distilled water and leave behind minerals that may be sold to offset treatment costs, Reynolds mentions. “Energy storage is such a huge market that everyone talks about lithium, but there are other minerals in the water that may be valuable, such as bromine, strontium, magnesium, etc.,” he says.
The cost to recover and transport these minerals will vary based on their concentrations, well location and market demand, Reynolds points out. “Selling minerals may not always be viable, but it would be a nice bonus to desalination’s other benefits,” he assesses.
Salt-Tolerant HVFRs
High-viscosity friction reducers (HVFRs) significantly reduce the amount of water needed to complete a well because they enable each gallon of fluid to carry more proppant than traditional slickwater designs, notes Zoraida Vazquez, Newpark Fluids Systems’ technology manager for stimulation fluids. She cautions that many HVFRs have been designed for use in freshwater.
“As the industry began moving away from building viscosity with gel and cross-linked systems, we saw a need for friction reducers that would work well in brines with high salt concentrations and divalent ions such as calcium, magnesium and iron,” she recalls. “This need is especially strong in areas where freshwater is expensive or unavailable.”
In response, Newpark has developed a produced-water-friendly HVFR that Vazquez says has exceled in both lab tests and the field. She cites third-party lab testing that evaluated the polymer’s elasticity and viscosity. “Even in extremely salty brines with TDS concentrations around 250,000 parts per million, the new HVFR retained its elastic characteristics and viscosity,” she reports. “These results suggest that the HVFR will have the carrying capacity to transport more proppant into fractures.”
Newpark Fluids Systems reports it has developed a high-viscosity friction reducer with a self-breaking mechanism designed to minimize the chance residual polymers will restrict production after the completion. In laboratory testing, this self-cleaning HVFR (A) outperformed other products even after a breaker was added.
Field applications confirm the HVFR’s effectiveness, Vazquez assures. A West Texas operator decided to use the HVFR in completion fluids containing 20%-55% produced water, she recalls. “The operator was able to pump proppant at higher concentrations,” she describes. “With each gallon of fluid carrying more proppant, the HVFR shortened the time required to complete each stage by 13 minutes and saved 12,000 gallons of freshwater for each stage.”
Vazquez mentions that the salt-tolerant HVFR degrades naturally, eliminating the need for breakers and the risk that residue will reduce fracture conductivity. She says such conductivity damage is common with conventional HVFRs associated with long polymer chains that have high molecular weights.
The new HVFR breaks down over time in elevated temperatures, Vazquez describes. To show how much that self-cleaning capability can increase production, she recounts a demanding application in the Permian Basin.
“The pressure pumper wanted a viscosity around 20 centipoise in a salty brine, which the self-cleaning HVFR achieved at loadings averaging 3.5 gallons per thousand gallons. Because the job called for pumping at 127 barrels a minute, the friction reducer also needed to endure high shear rates,” Vazquez relates. “We were able to meet these requirements with HVFR concentrations as low as 0.3 gpt.”
The three wells treated with the HVFR exceeded expected production by 150% and had the highest oil production within a three-mile radius, Vazquez reports.
Water-Based Drilling Mud
As operators look for ways to improve environmental performance and minimize diesel costs, many are evaluating whether they can switch from oil-based to water-based drilling mud, says Pawilai Hallmark, Newpark’s head of drilling fluid research and development.
“Water-based fluids often use plant-based additives that are safe, biodegradable and renewable,” she says. “The cuttings can be land farmed or disposed of at nearby locations, which limits trucking costs and the associated emissions.”
In many applications, WBMs speed drilling, adds Travis Vordick, a technical sales engineer. “Oil-based fluids generally need a substantial amount of weighting material. Add in the low-gravity solids the mud picks up from the formation, and this material can generate quite a bit of friction,” he says. “With a WBM, we can get most of the necessary density from chlorides. The reduction in solids–and therefore friction–enables faster pump rates.”
To illustrate the acceleration, Vordick cites a case study in which Kaiser Francis Oil & Gas compared 12 Wolfcamp wells drilled with a novel WBM to 12 wells using nonaqueous fluids. The average time to drill the lateral fell from 13.39 days to 5.58. The fluid also cost less, which helped cut the overall cost for each foot from $9.89 to $8.38.
The next-generation WBM uses a biodegradable polymer that serves several purposes, Hallmark says. “The polymer provides viscosity, fluid loss control and shale inhibition,” she details. “Using a single additive to perform three functions simplifies logistics and on-site work.”
As a biobased product that also sees use in the food and drug industries, Hallmark says the polymer is widely available. “We have adapted it to increase its salt and temperature tolerances. In many areas, these tolerances are high enough we can build mud with produced water,” she comments.
That capability reflects a multiyear effort to expand produced water reuse, Vordick notes. “In arid regions such as West Texas and New Mexico, water is scarce but vital to agriculture,” he says. “If we can figure out how to use produced water economically, it will benefit everyone.”
In most areas, Vordick acknowledges that using produced water in drilling muds costs slightly more than relying on manufactured brines or freshwater. He says that may change as regulators restrict access to freshwater and the technology continues to improve.
“Infrastructure is another piece of the puzzle,” he comments. “Sometimes we can pump produced water through temporary poly pipe, but on most sites, we still need to truck it in, which can make well water that is on location or nearby more affordable. I hope the economics will shift toward produced water as pipeline networks grow.”
Midstream Infrastructure
The conversation around water management is evolving rapidly, says Michael Dyson, chief executive officer of Infinity Water Solutions. “When we sat down with operators a few years ago, the conversation often focused on the benefits of recycling produced water,” he recalls. “That conversation does not happen anymore. Operators are keenly aware of recycling’s benefits, so their primary question is how quickly they can implement recycling in their operations.”
Pipelines and storage facilities will be critical to recycling’s growth, Dyson argues. “On any given day, some operators experience a flood of produced water that far exceeds their needs while others experience a drought of source water. With pipelines, storage and the right treatment technologies, we can take excess water from one area and send it where it is needed,” he outlines.
Toward that end, Infinity has built a water sharing network that covers 150,000 acres in the southeast corner of New Mexico. “We started with a singular truck facility off Highway 128 in New Mexico. Through a four-mile pipeline, this facility now connects to our full-state recycling facility, the Mills Ranch No. 1, which can process 75,000 bbl/d of produced water. When we finish with the last bit of storage there, it will be able to hold as much as a 2.5 million barrels.”
To simplify produced water reuse, Infinity Water Solutions is building a network of treatment and storage facilities linked by pipelines. According to the company, this infrastructure will improve recycling’s economies by sending excess produced water to areas with unmet demand.
By year-end, Infinity plans to bring on line a third facility with the working name Mills 19. Like the Mills Ranch No. 1, this facility will be able to process 75,000 barrels a day and store more than 2 million barrels, Dyson describes. He says an eight-mile pipeline will link the facility and Mills Ranch.
“When the Mills 19 enters service, we will have three networked facilities, each of which can receive, treat and store water,” he says. “Because they are connected, we can use water from the Mills 19 to replenish storage in the Mills Ranch No. 1 or vice versa. This flexibility will let nearby operators source water from a local facility to reduce transportation costs.”
Next year, Dyson says Infinity plans to build a storage and treatment site south of the existing network. Dubbed BAR No. 1, this facility will connect to the company’s existing network through a 28-mile pipeline. “As the market encourages or demands, we will continue to build out additional facilities. We envision any number of connections spidering off the main trunk line,” he says.
In addition to expanding its infrastructure, Dyson says Infinity is developing treatment technologies. For example, it has a patented process for introducing ozone, an oxidizer that kills bacteria and other contaminants. “This process distributes the ozone more evenly, but it is more expensive than standard techniques, so for now, we reserve it for water that is difficult to treat,” he says.
Dyson points out that the Permian Basin produces more barrels of water than oil, with some estimates putting the ratio at six to one. “We are far from the only ones innovating in this space,” he stresses. “At every stage of water treatment and transportation, there are smart people collaborating on better solutions. We all recognize that managing produced water efficiently will have phenomenal benefits.”
Dyson says broadening produced water applications will be key. “One of the biggest challenges of managing the water is location; it may not be needed where it originates,” he illustrates. “Transporting large volumes across long distances can be expensive. By making produced water attractive to farmers and other industries, we can find markets for it closer to the source.”
Remediating Wells
Remediating damaged wells using modern chemistries can pay out quickly, says Trent Kostick, director of stimulation services for North America at STIMWRX, a service line of Jacam Catalyst under the umbrella of CES Energy Solutions. “Remediation treatments can repair new wells that are underperforming because of completion/workover damage or revive stripper wells that may otherwise have to be suspended or abandoned,” he says. “We also remove damage mechanisms that candidates sometimes exhibit as a result of workovers or improperly applied treatments.”
It is all about the art of designing the right treatment and deploying it safely and economically. “Our goal is to give the operator payout in a couple months, if not days or weeks,” he comments.
Recent advances in chemistry are accelerating paybacks, Kostick says. As a case in point, he mentions acid treatments. “Many acid systems still pair hydrochloric acid with solvent, a concept that originated in the early 1900s. We have come a long way since then,” he says. “Some of the most effective Jacam Catalyst acid systems include nanosized molecules smaller than 100 nanometers in diameter. These nonionic interfacial tension reducing molecules penetrate deeper into the reservoir, which ultimately allows formation fluids and natural gas to flow more efficiently into the wellbore.”
To remediate a Bakken horizontal that had restricted production (most likely from formation fines in the lateral and near reservoir), STIMWRX deployed a proprietary nanosurfactant technology. Six months after treatment, the well’s oil production had increased 800% and its gas production had doubled when compared with the three months before the treatment, STIMWRX relates. The company says the treatment, like most of its restimulations, cost less than $20,000.
Kostick adds that Jacam Catalyst’s enhanced acid systems achieve more with less. “This applies to other stimulation chemistries as well,” he says. “In many cases, we can perform a technologically advanced treatment with 40%-50% of the chemical volumes typically required. This improves operator economics by decreasing the number of trucks on the road, time on lease and downtime, which often directly correlate to increased ESG performance.
“The more efficient chemistries tend to have quicker payouts and greater longevity,” he reports. “In treatments where a traditional acid job may boost production for only a few months, we often see significantly higher gains for many months or even years. We often completely alter the production trends, resulting in additional reserves over and above the timely payout.”
The enhanced acid stimulations also can improve disposal/injection well performance, economics and capacity, Kostick reports. “On a recent application, we reduced injection pressures 20%, which in turn increased the saltwater disposal well’s injectivity almost 120%,” he illustrates.
Rigless Deployment
The treatments pay out quickly in part because they rarely involve bringing a rig on site to pull tubing or downhole equipment, Kostick says. “To differentiate, we have engineered rigless applications that are noncorrosive to downhole jewelry and can be pumped with a low-rate pressure truck from surface,” he says. “Most jobs now include our proprietary formation-friendly diversion systems between stages to keep the product from simply flowing toward the path of least resistance.
“After the treatment is deployed, we let it soak in for a predetermined period (typically overnight). Then the operator can flow the well back through the bottom-hole pump and then through pipelines and facilities without issue,” he says. “In many cases, the entire job can be done for $10,000-$15,000.”
Instead of standard diverters such as benzoic acid flakes or rock salt, which typically are mixed on site, the treatments use a nondamaging gel diversion system that arrives prebuilt, Kostick mentions. “The gel breaks easily and quickly within hours of the application, which lowers the risk of setbacks during the application process.”
This new generation of gel diversion can be pumped at lower rates near two barrels a minute rather than the typical 10 barrels a minute, Kostick continues. He explains that the gel diversion conforms 360 degrees to fill the entire liner. In contrast, flakes and salts can fall to the bottom of the liner unless they are pumped at higher velocities.
According to Kostick, STIMWRX developed the diversion technique during the early Covid-19 pandemic downturn. “In the past two years, we have completed thousands of wells with this technology, and it has been a game changer from an economic success standpoint,” he reports.
Rigless restimulations have become sufficiently reliable that some of the largest operators now are creating a separate budget category for them, Kostick observes. “These companies realize the stimulations can significantly alter their declines, and in many cases, improve reserves evaluation and add value to the bottom line. Instead of treating a few wells in a field, they often move to hundred well projects and then take those successes into adjacent or offsetting fields.
“We have completed thousands of treatments across Canada and the United States. Most of them target horizontals rather than verticals because the horizontals have more reservoir potential to unlock,” Kostick relates. He says the company tracks every treated well’s performance, allowing it to provide relevant case studies to operators who are considering rigless stimulations.
STIMWRX is pioneering safer silica dissolvers, Kostick reports. “Today, the chemicals capable of breaking down silica come with several safety risks,” he says. “We have developed a novel silica breaker that has only a fraction of the hazards associated with hydrofluoric acid and other alternatives.
“We have also recently commercialized a new oxidizer package for remediating damaged polymer injection wells,” he continues. “These packages de-oil and degrade the target polymers while cleaning the formation face and potentially removing some mineral scale. Initially, we are successfully deploying these packages to help operators maintain polymer injection wells. Eventually, we believe they may be a solution to remove certain residual polymers after completions on wells that don’t meet type curves.”
For other great articles about exploration, drilling, completions and production, subscribe to The American Oil & Gas Reporter and bookmark www.aogr.com.