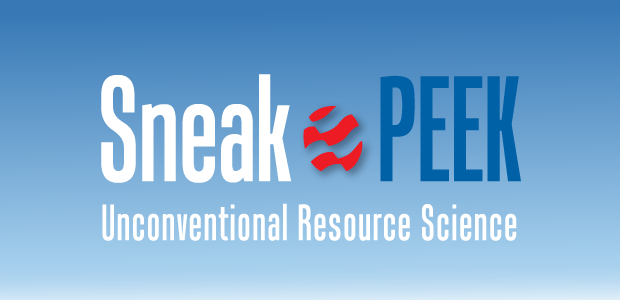
Pressure Pumpers Develop New Ways To Run On Natural Gas
By Colter Cookson
Investors, employees and the public expect the oil and gas industry to meet high standards. As they help deliver everything from electricity to the materials for cell phones, toys and tires, oil and gas companies must generate attractive returns while minimizing their operations’ environmental impacts.
If hydraulic fracturing fleets are any indication, the industry is embracing that challenge. In addition to optimizing the performance of existing equipment, pressure pumpers gradually are replacing the oldest portions of their fleets with modern marvels that get more from every ounce of fuel they consume.
According to Ron Gusek, president of Liberty Energy, next-generation frac spreads have a common goal: They are designed to run partly or entirely on natural gas rather than diesel. Natural gas costs less than diesel and produces fewer greenhouse gas emissions and very little particulate matter, Gusek explains.
Another factor influencing emissions is engines’ thermal efficiency, a measure of how much of the fuel’s energy is converted into valuable work rather than heat. He mentions that many of the diesel engines driving frac pumps have a thermal efficiency around 36%, meaning they only harness about a third of the fuel’s potential.
Liberty is field testing pumps that use a natural gas engine with a thermal efficiency around 45%, Gusek relates. “With these engines, we will be able to burn 25% less fuel and have 25% lower emissions,” he estimates.
The extra efficiency augments the already strong benefits of transitioning to natural gas, Gusek says. “The cost of a diesel gallon equivalent of natural gas is less than half the price for each gallon of diesel,” he says. “For a fleet that operates 300 days a year and consumes 20,000 gallons a day, the savings can translate to $50,000-$60,000 a day, or about $20 million a year.
“By retaining the majority of the fuel savings achieved with the new technology, we can give customers a next-generation, natural-gas-powered frac fleet without increasing their costs,” Gusek envisions. “That is fantastic for operators who want to consume natural gas and shrink their environmental footprints.”
Reducing Costs
One of the keys to the shorter payback associated with Liberty’s new pump is that each trailer requires fewer pieces of equipment. “Normally, if we want to run entirely on natural gas, we would use a pump that is connected to an electric motor. The motor would get power from a generator on a separate trailer,” Gusek describes. “Instead, the new pump connects the natural gas engine directly to the transmission, eliminating the need for a separate power generator and the power-handling equipment that links it to the motor.”
Liberty Energy is field testing a hydraulic fracturing pump design that allows more horsepower to travel from the engine to the pump. The company says the more efficient design will reduce construction and deployment costs for natural gas-powered fleets.
Alongside reducing construction and deployment costs, the simpler design helps cut emissions. “An electric pump takes energy from the natural gas, turns it into electricity for the motor and then uses the motor to convert that electricity back into mechanical energy,” Gusek illustrates. “Some of the energy gets wasted during each step.
“The new pump skips the transformation from mechanical to electricity and back to mechanical energy, meaning more horsepower makes it all the way to the pump,” he contrasts. “The increase in fuel efficiency and reduction in emissions, coupled with lower costs and other operational benefits, makes it an attractive investment complementary to our suite of fully-electric technologies.”
Those operational benefits include generating electricity for on-site equipment, Gusek mentions. “The natural gas engine the new pumps use is designed to run a genset,” he describes. “To use it in a frac fleet, we had to find unique solutions to overcome some technical challenges.”
In its traditional application, Gusek says, the engine expects to start with no load and gradually ramp up until it reaches a steady state. In a hydraulic fracturing fleet, it does not have that luxury. “If we are pumping at a treating pressure of 10,000 psi and need to bring another pump on line, we cannot turn on the engine with no load and step upward. It must handle 10,000 psi,” Gusek explains.
The solution, he continues, is to create a false load that forces the engine to increase output until it is ready for the real load. The first prototype pump simulated load using a water brake that posed reliability issues. “We replaced the brake with an electric motor/generator, a bidirectional device that produces mechanical energy if we put electricity into it or electricity if we put mechanical energy into it,” Gusek relates.
“While the primary purpose of the motor/generator is to create a false load, we can use some of the engine’s horsepower to create electricity for the cooling system and other equipment on site,” Gusek says. “If we want 2,800 or 2,900 horsepower from the pump but the engine is producing 3,300, we can harness the excess to generate electricity.”
Each hybrid pump might produce 100 or 200 kilowatts of electricity on a steady basis, Gusek details. “We envision a location with 10 of these pumps delivering 28,000 or 29,000 horsepower while simultaneously generating a megawatt or two of electricity for the pad,” he says. “That would allow us to electrify backside equipment such as the blender, hydration unit, chemical injection system, sand handler and wireline unit. On top of that, we might even have enough electricity to run one or two fully-electric pumps.”
According to Gusek, such electric pumps compensate for the natural gas hybrid pumps’ biggest limitation: Engines with no throttle control, meaning they are either at idle or running at their full speed of 1,500 rpm. When the pump needs to increase or decrease its rate, it must shift through gears, with each shift changing the rate by a barrel or two. Gusek points out that frac jobs often require more precise and rapid changes.
Enter Liberty’s fully-electric pumps, which Gusek says support near-infinite rate adjustments. “Most of our future fleets will have a combination of hybrid and fully-electric pumps,” he forecasts. “The less expensive hybrids will provide baseload power, while the electric pumps will give the fleet the flexibility to handle transient loads and dial in the rate.”
Fully electric and dual-fuel fleets will still have a place, Gusek predicts. “Ultimately, the goal is to give operators the ability to consume natural gas during hydraulic fracturing. The equipment we build will be based on their needs,” he indicates. “Some operators expect to generate enough electricity on their grids to power a frac fleet, in which case they will want a 100% electric fleet.”
Gusek predicts that scenario will be most likely in the Permian, where some operators have large, contiguous acreage positions and enough activity to justify investing in a private grid for drilling rigs, production facilities and frac equipment.
“In the opposite scenario, where the operator expects to have no electricity, we anticipate deploying fleets with a much higher percentage of hybrid natural gas pumps,” he says. “Other fields will be somewhere in between, with enough power available to run a few electric pumps. In that case, the hybrids will fill any gaps and deliver the fuel savings associated with efficient natural gas engines.”
Sourcing Gas
Even when natural gas prices were much higher, there was a strong economic case for using dual-fuel and electric fleets. As gas prices have pulled back, those economics have only become stronger, says Chris Fournier, director of equipment engineering at ProFrac Services. “Each Mcf of gas can displace about eight gallons of diesel. When gas is below $3 an Mcf and diesel is above $4 a gallon, the savings add up quickly,” he reports.
Fournier adds that both fleet types cut greenhouse gas emissions. “The biggest constraint around dual-fuel and e-fleet adoption is gas availability,” he assesses. “In a field without ready pipeline gas, compressed natural gas will need to be brought in, or field gas will need to be treated so it can be used. Both options, however, add costs that can impact the economics associated with displacing diesel.”
In oily plays that generally produce rich gas, bringing in CNG tends to be more affordable than conditioning field gas, Fournier advises. “In West Texas, almost all our dual-fuel fleets run on CNG,” he illustrates. “The field gas is rich and low-pressure, so to utilize it, we need to compress it, condition it and then bring the pressures back down. Tally those costs, and it usually makes more sense to run on CNG.
“Over time, the industry will push to use more field gas in basins that traditionally use CNG,” he predicts. “Many of these plays may have takeaway capacity constraints, which means operators will have to transport associated gas by truck, flare it, restrict their production or find a way to use the gas. At today’s prices, repurposing the gas can make more sense than paying to transport it.”
To render field gas usable, companies often condition it or blend it with CNG, Fournier outlines. In some plays, he says, electric fleets can simplify conditioning because their power generators tolerate higher Btus than dual-fuel engines. “Sometimes it only takes minimal conditioning to make field gas suitable for a generator,” he says. “We may have to run compression to get the gas to the higher pressures e-fleets require, but that can cost less than handling both Btus and pressure.”
E-fleets’ tolerance for rich gas can enable operators to move away from diesel in plays where CNG is unavailable or costly, Fournier adds. “That will be a huge benefit, especially in basins that may have takeaway issues in the future,” he says.
This gas conditioning skid from ProFrac Services is enabling a hydraulic fracturing fleet to run on field gas by removing contaminates such as liquids, condensates and chemicals. These skids may become more common as the industry looks for ways to use stranded gas.
Optimizing Conditioning
Fournier points out that ProFrac provides gas conditioning services with equipment it manufactures in house. He says internalizing gas conditioning has helped the company achieve high substitution rates reliably.
“The biggest hurdle when running a dual-fuel fleet is getting consistent pressure across the system,” Fournier details. “The hard starts and stops that occur at the beginning and end of each stage make for a strenuous environment, but we can compensate for that with the right pressure regulation system. Designing that system is much easier when we know the equipment, the demands placed on our pumps, and the conditions we will encounter on each pad.”
To run on field gas, fleets must account for changes in its composition during a job. “In an area where operators are drilling into several formations, the quality of the gas we pull from the gathering system can swing based on which wells are producing at a given time. We also have to watch for liquids, condensates, pipeline chemicals or other contaminants,” he explains.
Monitoring gas quality is essential for safety, Fournier emphasizes. “The second we sense gas outside the range we have identified for the specific pad and equipment, we automatically shut off the gas and switch to 100% diesel. This protects the engines before any catastrophic damage occurs,” he assures.
Instead of monitoring Btu levels with gas chromatographs, ProFrac uses meters from JP3 Measurement LLC. “Chromatographs work great, but they require more time to get readings and often need to vent the sample gas they pull,” he observes. “With our monitoring technology, we can get a real-time view of the gas stream, and we have no emissions because we do not need to vent.”
While gas conditioning equipment has become more efficient and reliable with time, Fournier says the biggest step-change involves digitization. “When dual-fuel fleets first kicked off, we had the ability to look at the gas coming into the pump and see how much gas individual engines were substituting, but we did not have great visibility into what was happening before the gas reached us,” he recalls. “Today, we can check every piece of equipment we are running remotely, which makes troubleshooting much faster.”
Fleet Diagnostics
With the right data, pressure pumpers can extend equipment life significantly, says Jeremy Frank, co-founder and chief executive officer of KCF Technologies Inc. “For most of the companies we have worked with, equipment life has doubled,” he details. “For fluid ends, it’s tripled. A decade ago, most companies would get 300-350 hours from a fluid end. Today, the average is well over 1,500 hours, and it’s not uncommon to see 2,000.”
Installing magnetic vibration and temperature sensors throughout a hydraulic fracturing spread can reveal ways to improve safety and efficiency, KCF Technologies reports. The company says the sensors have helped many fleets double or triple equipment life.
These gains are partially attributable to placing magnetic sensors on pumps’ exteriors to monitor vibration and temperature, Frank notes. He likens the sensors to experienced hands’ practice of touching pumps to detect signs of trouble.
“The activity inside a pump can be very destructive,” Frank observes. “One of the most common problems is cavitation or knocking. When the plunger pulls backwards to draw fluid into the pump but isn’t seeing enough flow, it creates a vacuum that vaporizes the liquid inside and causes it to expand rapidly. This explosion of water vapor is extremely destructive to the consumables inside the pump, including the borehole and the valves and seats.
“The magnetic sensor on the outside may not be able to detect cavitation directly, but through years of hard work in partnership with experts in the field, we can correlate its temperature and pressure readings with cavitation and other issues,” Frank reports.
According to Frank, that capability can reveal or confirm observations that help redefine best practices. “For example, 10 years ago, when many spreads had both triplex and quintuplex pumps, we noticed that cavitation and other destructive events were more common and severe on the triplex pumps,” he recounts. “At the time, most people expected triplex pumps to be stronger, simpler and more robust. That is probably true in general, but during hydraulic fracturing, other factors caused the pumps to encounter severe conditions.”
Although it took time to determine those conditions’ root causes, the lesson was obvious much sooner, Frank recalls. “The quintuplex pumps ran smoother, so most of our customers switched to them,” he clarifies.
In addition to monitoring pumps, KCF can place sensors on other equipment. Frank says optimizing the spreads’ fluid dynamics can entail looking as far back as the blender discharge pump. “One of the simple but previously unseen realities we discovered is that many fleets were not delivering sufficient pressure from the blender discharge,” he reveals. “If we had only watched the pump, we never would have realized the entire system needed more flow.”
Through machine learning algorithms, the company’s software quickly converts sensor data into useful insights, Frank assures. “One of the most important real-time insights these algorithms generate is spotting washed out valves,” he illustrates. “Once that happens, the fluid end no longer contains all the pressure that develops inside. That is extremely destructive to the fluid end, and it can lead to dangerous situations if other failures happen at the same time.”
To avoid those situations, fleets back out of a pump or at least reduce its load once they detect a washout, Frank notes. “A vibration sensor with the right intelligence can identify a washed-out valve and seat’s signature, then send an alert so the fleet can adjust quickly, which minimizes safety risks and equipment damage,” he says.
The sensors also warn crews about power end problems such as cracked teeth, misaligned gear sets or failed bearings, Frank adds.
By protecting equipment, the real-time alerts can save lives. “The most dangerous and stressful situations in the field usually involve unplanned events or downtime that put people in an emergency mode,” Frank explains. “As field hands who initially express skepticism about our technology see those disruptions occur less frequently, they often become advocates for it.
“Pressure pumping is an extremely complicated fluid dynamics problem,” he reflects. “One of the most important areas we study is how the slurry flows through the missile or manifold and into the frac pumps. We spend a lot of time simulating, testing and observing various flow path designs to come up with improvements that are theoretically sound and robust enough to work in the field.”
Even something as seemingly straightforward as the suction hoses’ diameter or the order in which pumps come on line can alter fluid dynamics for better or worse, Frank says. “We are nowhere close to coming up with perfect solutions,” he assesses. “It can be tempting to think that because fleets have come so far, but there is so much more to understand.”
That applies not only to hydraulic fracturing but also to drilling. “We are leveraging the expertise from frac fleets and other industries to solve problems on drilling rigs,” Frank mentions. “For example, mud pumps’ undesirable behaviors often have root causes similar to those on frac pumps, and the machinery on a top drive resembles traditional rotating machinery with gearboxes, motors and fans.”
Increasing equipment durability and energy efficiency can be a huge win for the environment, Frank comments. “With a 2,500 horsepower pump, even a relatively small improvement in energy efficiency can lead to massive savings,” he says. “Extend similar improvements across manufacturing and other industrial sectors, and the effect can be tremendous. In fact, optimizing industrial equipment will have a much greater impact on the world’s greenhouse gas emissions than the global switch to electric vehicles.”
For other great articles about exploration, drilling, completions and production, subscribe to The American Oil & Gas Reporter and bookmark www.aogr.com.