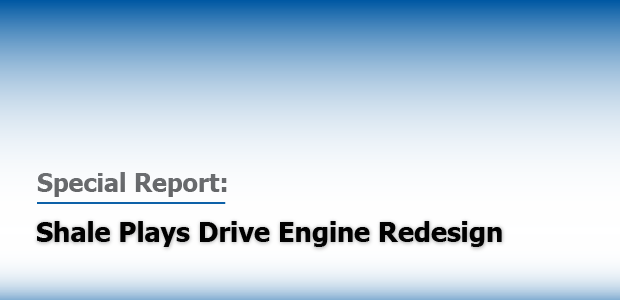
Compression And Processing
Shale Plays Drive Engine Redesign
By Kenneth C. Hall
PEORIA, IL.–By clustering wellheads that were once isolated, horizontal pad development techniques in unconventional resource plays have altered the specifications for wellhead gas compression from small units, often less than 250 horsepower, to much larger packages frequently requiring at least 1,750 HP.
At the same time, regulatory standards for natural gas engine emissions have tightened substantially in many areas. Operators that only 10 years ago may have regarded emissions controls an unnecessary expense are now well-versed in selecting and operating these systems, and the regulatory push for ever-tighter emission limits is keeping engine manufacturers on the hunt for cost-effective technologies to help them evolve designs to achieve lower emissions.
Perhaps the one requirement that has not changed for gas compressor engines is the need for flexibility. The engines used in compressor packages in unconventional plays require the flexibility to operate over a wide range of gas qualities, in a wide range of conditions and with a high degree of reliability. By using local raw gas as fuel, gas compression units avoid charges for fuel treatment and transport, but at the cost of leaving perhaps the most important engine design parameter–the fuel–highly variable. Add the extreme operating conditions found on many sites and the challenges in developing next-generation compression engines becomes more apparent.
The key to simultaneously managing all these challenges in an engine development program is discipline. By maintaining focus on key aspects of the process throughout each stage, and periodically reviewing progress along the way, a design team can ensure the product it is working toward will meet the demands of the intended application. To illustrate this approach, this article examines the process used to introduce a significantly updated model of an existing gas compression engine to accommodate the new requirements of onshore resource plays.
The larger-displacement engine had been well established in the gas compression market for several years, but patterns emerged regarding customer requests for expanded capabilities to accommodate shale plays. This need for an expanded performance envelope formed a solid basis for launching a development program to update the design.
Gate-Driven Process
The first step in converting customer requirements into a new engine’s operational attributes was identifying all stages of the process, considering it would involve a lot of widely varied activities. Those stages were defined by the activities that must be completed during each portion of the updated compressor engine design process, and the necessary discipline was applied by separating each stage with “gates.” Each gate constitutes a milestone in the process and includes a review of the progress that must be satisfactorily completed to that point before it can gain approval to proceed to the next stage.
The gate-driven process is highly interdisciplinary in that all areas of the business–from market research to engineering, manufacturing and supplier management–are involved at each gate review, with the authority to call out potential issues from their respective areas of expertise. Periodically raising visibility to all program stakeholders keeps the direction on target in all of the critical measures that apply.
For the case study example, eight gates–with each carrying specific goals for completion–were defined:
- Launch, defining the “what” and “when” of the new engine update;
- Concept definition, defining “how” the new engine will meet its requirements;
- Concept development, optimizing “how” through focused technical and market studies;
- Prototype creation, transitioning from concept to a working model for further study;
- Prototype development, which evolves the working model from proof-of-concept to ready-to-build;
- Pilot, which seeks to finalize the production and supply chain processes while simultaneously validating the new product’s quality and reliability attributes;
- Production, confirming the engine is ready for release to the market; and
- Reflection, providing a look back on the results of the engine’s introduction, seeking verification that it has realized its goals and seeking lessons learned that may be useful for future programs.
Even Leaner Combustion
The path from launch to the next two gateways brought into focus the chief areas of the challenge at hand. While ambitious goals were set for fuel flexibility and an increased site performance envelope (minimized derating for site altitude and ambient temperatures), perhaps the most aggressive goal was to simultaneously achieve lower oxides of nitrogen engine emissions. The existing engine was a lean-combustion design, using pre-chambered combustion to achieve a stratified charge effect for lowered NOx. Reducing NOx emissions even further requires even leaner combustion, making combustion variability the key consideration.
All components of the new combustion system–turbochargers, air/fuel mixing, intake charge cooling and combustion control feedback–had to achieve their tasks more consistently to enable a successful outcome. The functional requirements presented at the concept definition gate became the starting point for the goals the design had to achieve. Further testing work confirmed the concept’s validity, providing a solid technical footing.
The technology incubator for this development program was the release of the next smaller engine family. It successfully demonstrated the effectiveness of “smart” air/fuel mixing valves when integrated with real-time NOx exhaust measurement. Coupled with this, the use of two-stage intake air cooling improved temperature stability, ensuring the incoming fuel/air mixture was consistent and repeatable (the key to a low coefficient of variability for combustion results across all of the engine’s cylinders). The responsiveness of these technologies enabled the engine to operate with smaller and shorter excursions from the performance mean, enabling the engine to achieve a much lower average NOx output.
In the context of certain regions’ prevailing emission regulations, a very low power-specific NOx output is critical on a large-displacement, high-power engine because it can impact an installation’s total accumulated NOx emissions significantly. In this case, these applied technologies combined to cut specific NOx emissions by 40 percent off the original target rate–a tremendous achievement–while at the same time increasing the power output and range of site conditions at which the engine could reach full performance. The demonstration of this strategy on a single-cylinder laboratory prototype engine was successful, and work began to create a full prototype engine on which to refine the pieces on a full-production scale.
Combustion Chamber
Although lower emissions were now possible, other changes were needed to widen the range of acceptable fuels significantly. This shifted the design focus to the combustion chamber. Piston geometry optimization was combined with altered cam events, which together were integrated with the improved turbocharger performance to create the needed margin against detonation and misfire. By this point, a version of this design had been available in the smaller engine. The key was finding the right combination for the larger platform, and to see precisely how far its performance could extend.
Simulation was used in these early design evaluations to accelerate decision making. A simple example of the value of these simulations is found in the efforts to optimize fuel line sizing for best performance across the wide targeted range of fuel energy values. A model was constructed to simulate system performance according to various line sizes. This allowed the team to identify a size that could maintain fuel flows at both extremes of the fuel energy range within the delivery requirements of the smart mixing valve, which was critical to consistent performance for all possible fuels. This simulated study highlighted a key design parameter without the time and cost of creating physical flow evaluation models.
With the fuel delivery system cleared for use with hydrogen sulfide in the fuel gas, the focus then moved to the mixing valve. Its function enables precise air/fuel ratio control under constantly changing conditions, and therefore constitutes a key to the engine’s high-performance, low-emissions design strategy. The supplier provided a version of the valve that is capable to an H2S concentration of 1,000 parts per million. This reached very close to the original target and was deemed an acceptable compromise. Now the H2S tolerance capability for the whole engine was set.
The design optimization prior to the prototype test engine build made extensive use of computer modeling of combustion and whole-engine performance. The models explored combinations of piston and cam geometries to make the best use of the available turbocharger performance map. The goal was to extend the usable fuel range to the high design target, selected to be the combustion equivalent of HD-5 propane. The modeling allowed many possible combinations to be narrowed to a much smaller set deemed appropriate for actual testing in a single-cylinder engine.
The performance data gathered from these single-cylinder test runs were used to correlate live testing to the computer simulation, and from that confirmation, one combination was selected to proceed to a multicylinder test engine. The test plan for the prototype engine was developed from the performance goals and specific areas of interest identified by the failure mode effects analysis (FMEA) process, plus details derived from experiences in past engine development testing. This full battery of operational and mechanical component evaluations formed the base line confirmation that the design was capable of delivering on all program targets for performance, reliability and durability.
‘Field Follow’ Validation
As each component was stabilized to a production-ready design, it was worked with its source of supply to prepare for full-volume manufacturing. At the same time, the performance testing results were used to promote the capabilities of the new engine to customers willing to put pilot engines into real-world installations. This “field follow” process was used to provide longer-term validation of the new design’s performance and durability.
While field follow validation work is expected to proceed without incident, its value is proven each time an issue comes to light. For instance, the external insulation for the exhaust manifolds unexpectedly failed to perform as expected during validation. The seemingly robust rigid box design did not hold up well in the high-vibration environment, an outcome that likely only would have appeared in this kind of extended-run test condition.
Once the nature of the insulation issue was confirmed and the root cause identified, design corrections resolved the issue. Under such circumstances, the corrections often need to be implemented in two tiers: interim corrective actions to get the operating field units back in service quickly, and permanent corrective actions that fit with the need for performance, durability, manufacturability and cost-effectiveness. For these exhaust shields, both actions focused on reverting to a more demonstrated soft-wrap insulation design that fulfilled all the requirements.
In the end, these final stages of development demonstrated that a significant advancement in engine performance had been brought to a market-ready condition. The new engine was significantly more powerful (+5.5 to 6.0 percent is typical) across a wider range of site operating conditions and used a significantly broader range of fuel compositions.
The redesigned engine expanded the fuel range to include notably more heavy hydrocarbons and inert gases in the mixture, introducing the possibility of using the engine in applications that would have challenged previous models. This very capability corresponded with operators’ needs in the unconventional gas plays that provided the impetus for this development work, so the final outcome was certainly a “mission accomplished.”
However, the redesigned engine exceeded the market imperative requirements stated at the program’s inception. Additional details were worked into the design to improve the customer experience with packaging the engine. Features previously unavailable on the engine, such as onboard cooling system thermostats or access to coolant flow for the compressor’s lubricating oil, became standard. The updated electronic engine management system enabled the development of new interface panels for improved user experience, and made a wealth of engine operating data available for engine monitoring and optimization to further extend the value of the installation.
But even beyond the increased power, altitude capability, fuel tolerance, ease of use and lowered emissions, the new work added a new capability for gas engine drivers of this type: the ability to easily adapt to prevailing operating conditions to deliver the maximum power available at any given time.
Ambient-Based Operation
Natural gas engines long have been marketed with ratings that vary according to the coolant temperature provided to the aftercooler. This relationship reflects the fact that lower air temperatures produced in the aftercooler result in denser air entering the cylinders. While operating at a controlled air/fuel ratio, more air in the cylinders enables more fuel to be admitted, and more fuel can be converted into increased power. However, engines were set up with a single rating reflecting the fixed aftercooler design temperature.
Taking advantage of the advanced computing power of modern electronics allowed the redesigned compressor engine to have a variable rating with the capability to produce more power when lower ambient air temperatures allowed. Added value was realized by enabling the engine’s control system to measure in real time the achieved temperature of the combustion air coming from the aftercooler. This allows the engine to provide a signal indicating its power potential under current operating conditions, making it possible to take advantage of the power available during cooler periods.
This variable rating system can be incorporated into the compressor package easily, since the signal provides the information needed to serve as feedback for automated compressor controls to utilize the increased power. By including in the package design variable volume pockets, the compressor can be equipped to vary the operating point to adapt to the engine’s changing power potential. Thanks to adjustment motors on those variable pockets, the compressor configuration can be adjusted in response to the engine’s load signal, making automated power optimization for varying conditions not only possible, but practical to implement. This ambient-based rating feature allows the installation to further maximize value by providing even greater productivity from a certain size of compressor package.
Successfully incorporating multiple new technologies into a single engine platform can be a difficult and time-consuming task. However, as this case study demonstrates, a robust and disciplined design and development process can enable significant advancements in engine performance and value while also allowing novel engine features to be incorporated into the design, such as ambient air temperature-based power ratings to increased compressor throughput by as much as 7 percent during periods of lower ambient temperature. This adds even more value to a gas compressor package that has been engineered with the capabilities to push performance standards to new heights in unconventional plays.
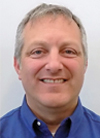
Kenneth C. Hall is the senior application engineer for gas compression within Caterpillar’s oil and gas marketing group. He has more than 25 years of experience with natural gas engines, with much of that time focused on the gas compression industry. Hall serves as a knowledgeable resource to Caterpillar’s dealers and customers worldwide for issues involving the selection, integration and operation of gas engines in compression applications. He holds a B.S. in mechanical engineering and an M.B.A. from Purdue University.
For other great articles about exploration, drilling, completions and production, subscribe to The American Oil & Gas Reporter and bookmark www.aogr.com.