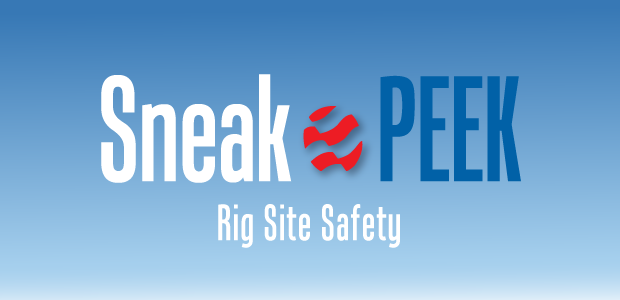
Training, Automation Improve Safety
By Danny Boyd
Drilling contractors have a long track record of leading safety. According to the International Association of Drilling Contractors, U.S. land drillers’ total recordable incident rate (TRIR) for the third quarter of 2023 was 1.69. To put that number in perspective, the U.S. Bureau of Labor Statistics reports that grocery stores had a TRIR in 2022 of 4.3, two and a half times as high.
The industry’s low TRIR demonstrates that worker safety remains paramount for drilling contractors and other upstream service companies. It’s a testament to how well upstream companies have maintained their safety cultures despite many seasoned hands retiring during the past few years, as well as how effectively they have managed the risks associated with longer laterals and zones with higher temperatures and pressures.
To take safety even further, many drilling contractors are deploying automation and robotics to minimize their crews’ exposure to risks. At the same time, service companies across the industry are developing more effective training and safety programs and tapping workers’ expertise to identify areas for improvement and reduce serious injuries and fatalities.
Field safety personnel play a critical role in service companies’ efforts to promote best practices and awareness, says Eric Baldridge, director of QHSE for RPC Inc. subsidiaries Thru Tubing Solutions, Cudd Pressure Control, Cudd Well Control and Well Control School. He emphasizes that safety managers continually impress on safety personnel the need for a service attitude toward employees.
“As safety personnel, we are not trying to be an authoritative figure as much as a helping hand in the field,” Baldridge clarifies. “We are out there to improve the daily work of employees, whatever that work may be. When that comes across, the relationship between a worker and a safety adviser changes and both get more done.”
Leveraging workers’ input and observations is one of the best ways to improve safety, Baldridge suggests. With that in mind, Thru Tubing Solutions (TTS) and Cudd Pressure Control (CPC) launched an initiative in 2022 to improve internal safety reporting and give crews on location more access to leaders.
“Under our new process, workflows involving a safety incident or anything requiring safety at all automatically include upper management,” Baldridge says. “That has been a huge help.”
In addition to reinforcing how seriously the company takes safety, Baldridge explains that involving upper management encourages workers to share concerns and suggestions because they know their feedback will reach someone with the power to make changes immediately, rather than needing to pass through multiple layers.
As part of the safety initiative, management also upgraded assessments for job applicants and made sure each applicant received a detailed explanation of job requirements from district managers and other local hiring officers.
Training Program
Efforts to instill and reinforce a safety culture, enhance internal oversight, and continually improve training programs are contributing to a reduction in recordable incidents, Baldridge assures. All TTS and CPC workers, whether veteran or new, undergo extensive in-house and online safety training that is tailored to the skill level needed for each job, Baldridge says. He indicates that the companies have a robust library of online courses ranging from safety and well control to human resources.
By encouraging employees to embrace safety training and improving internal safety reporting processes, Cudd Pressure Control and Thru-Tubing Solutions report they are significantly reducing their incident rates.
OSHA general safety courses taken through an online learning management system cover fall and respiratory protection, hearing conservation, forklift operation and numerous other topics. In-house instructors provide hydrogen sulfide certification, CPR/first aid training and the eight-hour SafeLand curriculum that most major and large independent operators require before allowing contractor employees on a lease, Baldridge describes. He adds that all employees receive routine safety briefings on job sites.
The company also provides National Commission for the Certification of Crane Operators-certified training for operating cranes, rigging and signaling, and CPC employees receive additional specialized safety training related to snubbing. To counter sometimes long waits at external commercial drivers’ license schools, the company established its own CDL school, which includes training on mountainous terrain to prepare drivers for various field conditions, Baldridge mentions.
Well Control School provides IADC/IWCF training for any employees who need this certification, Baldridge assures. He says the school also maintains a knowledge-based library that offers on-demand training. This resource gives users access to more than 400 instructional videos, encompassing all well control objectives mandated by industry standards.
After initial training, new employees work with mentors assigned by district managers for six months. Every worker is evaluated at one month, three months and six months, but new employees are evaluated daily, Baldridge notes. After six months, if district managers consent, these employees can be released to work on their own.
Written evaluations are sent to district managers and company offices on an internal electronic matrix to identify any need for additional training. At any time, no more than 30% of workers at any location or department can be new, or short-service employees with fewer than six months of experience, he says.
Employees are encouraged to buy into safety training through a tier-based safety incentive system, Baldridge continues. Workers within groups or districts without a recordable injury or at-fault vehicle accident for the month receive a gift. A BISON (Behavior Improvement Safety Observation) program allows employees to report potential safety issues through a QR code-based system. Thus far, the company has had over 2,000 responses.
“We want employees to have ownership in regard to safety at all times,” Baldridge says. “Our safety programs also give us good data points to share with our customers. Safety is a universal objective, so we are very transparent and share results with all our customers. Since this tier-based incentive program was put in place earlier this year, we have cut our incidents in half.”
Safety Commandments
To mitigate risk and protect employees, Helmerich & Payne teaches its teams to uphold 10 safety commandments, or LifeBelts, that must never be compromised, says HSE Director Micah Backlund.
The Tulsa-based drilling contractor, which had about 150 rigs operating across the United States at the end of September, developed the LifeBelts as a way to provide guidance on a wide range of safety-specific issues, including the use of electronic devices, vehicle safety, lockout/tagout, pre-job planning, buffer zones and barricades, tie-off when working at heights, how to handle tubulars safely, staying out of the path of moving equipment, inspecting and securing equipment to prevent dropping objects, and using permits as required.
To limit employees’ exposure to safety risks, Helmerich & Payne has introduced a remotely-operated torque wrench. According to the company, the wrench consistently delivers the high makeup and breakout torque needed to ensure connection integrity.
Backlund stresses these LifeBelts are not intended to be used as a “gotcha” for employees that make simple mistakes. Instead, they are a way to clearly communicate H&P’s expectations for safe work.
“We are all human and make mistakes, but if we try to hide those mistakes instead of learning from them, that is not a healthy way to operate,” he says. “We, as a company, do not tolerate dishonesty, and we incentivize engagement in our processes.”
Employees are rewarded for observing and reporting practices that can lead to injury or death. Rewards can be as high as $500, including $100 given at the rig level, $200 awarded by vice presidents and $200 more given out by the company president, Backlund details. Since 2019, he adds, H&P has included a 50% premium for certain reports to encourage employees to get engaged with the company’s annual HSE goals and improve safety compliance in a specific area.
All new employees undergo work and safety training before they go to the rig. This training includes classes on general safety awareness and OSHA-mandated courses on material handling, equipment operation, fire safety, first aid, emergency response, bloodborne pathogens and other topics, Backlund describes. New hires are taught in class by a company instructor, and once the employee arrives at the rig, weekly training is provided by rig leaders, including rig managers and drillers.
As part of new employees’ continuous development, they are assigned a mentor on the rig who is responsible for providing guidance and feedback. This formal mentor must sign off on a digital checklist of training items to help ensure new employees are progressing as required.
If progress is slow in some areas, the employee receives additional training to get caught up, Backlund says. On-site training includes hands on training for equipment, as well as digital training sessions and quizzes, the results of which are stored electronically in H&P’s learning management system. Using this system, rig managers, drilling superintendents, executives and other company leaders can track employee development and provide additional support when needed.
With 14-day work schedules, employees generally receive 26 on-site safety training sessions a year, Backlund notes. During each tour change, rig managers, in conjunction with representatives of other contractors and operators, conduct meetings to review ongoing work and any safety issues before handing the work off to the incoming crew. These meetings sometimes include electronic Job Safety Analyses that contain links to videos on critical points for preventing serious injuries and fatalities.
Rig supervisors are required to complete a digital checklist, referred to internally as a Flex Check, that Backlund likens to a pre-flight checklist in aviation, but that is designed to prevent serious injuries or fatalities. As part of this checklist, supervisors verify that required tasks for various procedures are done by assigned employees. The list shows which employees are qualified to do which tasks. Over time, new employees work with mentors, watch training videos and review study bulletins to expand their qualifications.
Automation
In addition to investing in training, H&P is deploying automation to reduce employees’ “red-zone” risks. This automation targets work around the rotary, which Backlund calls the bullseye for anyone interested in preventing serious injuries on drilling rigs.
Drilling automation began decades ago, with significant milestones in automation including the development of AC-powered rigs, the introduction of iron roughnecks and the move from traditional rotary tables to top drives, he recalls.
Now, the company has introduced a remotely operated, higher-torque floor wrench capable of making and breaking connections on the larger-diameter pipe longer laterals require. The wrench can apply 100,000 foot-pounds of makeup torque and 120,000 foot-pounds of breakout torque, Backlund details. He says it is much safer and more consistent than asking rig crews to labor with floor-operated hydraulic tongs, manual tongs or chains.
A new retractable slip lifter eliminates most of the situations in which rig crews are required to pull and set slips, Backlund says, and traction-control floor mats reduce the potential for workers to slip on the rig floor. Existing technologies, which control weight on bit, torque and pressures on mud motors, have proven successful at helping reduce tool failures and associated bit trips, which ultimately limits the potential for an employee working on the rig floor to sustain an injury, Backlund reports.
Over time, the company aspires to automate all pipe handling activities, he previews. However, this increase in automation does not come alongside plans to reduce conventional rig crew size. Instead, crew members’ roles and responsibilities will evolve to reflect the more technical skills required to maintain and operate the automated equipment, Backlund says. As part of that evolution, crew members will receive additional technical training to ensure they have the skills necessary to meet the challenges associated with these significant improvements in equipment.
“Automation is the future of the industry,” Backlund assesses. “We will be able to run all those technologies remotely, whether it is from the driller’s cabin or next to the rig floor.”
Robots’ Power
To enhance safety on the rig floor, Precision Drilling is incorporating robotics to execute the repetitive tasks currently carried out by employees, says Rob Houston, vice president of rig technology and service delivery for the Calgary-based contractor.
As part of its quest to prevent injuries and fatalities, Precision Drilling says it incentivizes employees to identify better ways to work that promote safety and consistency.
“Since the introduction of top drives and iron roughnecks, current rig floor workflows have been perfected by experienced rig crews. It is important to maintain these workflows when incorporating robotics to maximize efficiency gains and our crews’ comfort level,” Houston says. “Drilling is demanding enough that it takes an entire rig crew and multiple service providers working together to avoid nonproductive time and stay on schedule.”
Houston says automation will enable rig crews to accomplish more. “This new deployment will allow most of the rig floor activities to be completed by one or two employees as compared with four or five today. This new bandwidth or time that is freed up will allow our employees to be upskilled to support the overall well construction process and provide efficiency gains never seen before in the industry,” he envisions.
Precision has been testing a third-party robotics offering on a test rig in Texas in preparation for rolling out its first commercial land rig robotics system in January, Houston says. “The number one hurdle we face when rolling out a new technology is reliability. When any deployment does not work as intended, it induces risks and frustration,” he comments. “Having multiple years of run time in a controlled environment allows us to treat the first commercial rig as a second deployment while incorporating the previous lessons learned.”
The company’s short-term goal is to automate 80%-85% of all rig floor activity using systems that complement the downhole automation it already has proven, Houston outlines. Toward that end, he says a partner company has developed a modular robotics offering that incorporates electric robots resembling those used in auto manufacturing, with multiple attachments and pivot points for performing a variety of functions on the rig.
The robotics deployment will include three robotic arms. One robot will handle all the work at the elevated platform (also known as the monkeyboard or fingerboard). This includes racking stands of pipe when the rig is pulling out of hole and bringing racked pipe forward to the elevators when it is going back in, Houston describes.
Two robots will operate on the rig floor. The primary one will perform tail-and-stab functions normally handled by the motor man or main roughneck. It will run on a track to gain the leverage needed to bring the bottoms of racked stands forward to stab in the box while going in hole or to rack pipe back when coming out, Houston continues. The auxiliary robot will provide the pipe stabbing guide and includes multiple attachments for cleaning and lubricating threads.
These robots will follow the same workflow people have perfected over the years, Houston reiterates. If a worker could not lift 600 pounds, neither can the robot. Instead, the deployment leverages existing equipment such as the top drive to hoist heavy tubulars. The rest of the rig floor equipment, including automated iron roughnecks, will continue to make up joints and break them apart, and the top drive will continue to be used to lift pipe out of the slips and run pipe in the hole, Houston adds.
Given the industry’s constant effort to drill deeper and faster than ever before, Houston predicts the demand for rig crews will continue to grow. He describes Precision’s robotics initiative as an exciting step change that will enable field staff to have an even bigger impact on well construction.
“Collaboration between all parties—the operator, drilling contractor, third-party service providers and our robotics partner—will be key to deploying robotics safely and successfully,” Houston says. “If commercialization goes as well as we think it will, the impact will be huge.”
Beyond Incident Rates
Jennifer Guidry, Precision’s vice present of global health, safety and environment, says Precision is embracing technology and automation as part of a safety program that incorporates the five principles of “human and organizational performance,” or HOP, popularized by Todd Conklin, a senior adviser at Los Alamos National Laboratory, and Bob Edwards, a military veteran, design engineer and maintenance expert who works closely with Conklin to help organizations learn from past events.
Guidry summarizes the five principles of HOP as follows:
- Even the best people make mistakes.
- How leaders respond matters.
- Blame fixes nothing.
- Context drives behavior.
- Learning is vital.
HOP suggests that companies that focus on preventing serious injuries and fatalities (SIF) should work to decrease risk and increase controls to fail safely. When mistakes occasionally slip through, the organization should avoid pointing fingers. Instead, it should figure out the contextual factors that undermined employees’ ability to notice and respond appropriately to risks, then mitigate those factors, Guidry outlines.
Contextual factors can include real or perceived pressure to complete work more quickly, variability in experience and skill levels, one-size-fits-all standards and procedures, generalized training, and equipment design and set-up, Guidry illustrates. She says identifying and addressing these factors is much easier when safety and operations work shoulder to shoulder rather than being viewed as separate functions.
To measure its progress on safety, Precision goes beyond recordable incidents. Citing statistical research showing that reducing recordables does not actually reduce serious injuries and fatalities, Guidry says the company now focuses on closing the gap between work as imagined and work as done and implementing critical controls. Precision measures SIF actuals, SIF mitigated and SIF potentials along with other leading indicators, she adds.
“We are designing and building our standard operating procedures, work instructions and hazard assessments to work as done, meaning we are designing work to the day-to-day realities of our workers,” she comments.
The HOP framework observes that workers’ reality (work as done) can be quite different from how the office designed the work (work as imagined). Guidry says developing procedures with a worker-centric approach ensures they reflect how often and quickly workers need to adapt given the variability in the field and the never-ending changes in tasks that need to be addressed to finish a job.
Instead of offering rewards for recordable-free or lost-time-free periods, Guidry says the company rewards employees for implementing process improvements, or better ways to do their jobs that create consistency and standardization. Examples include figuring out how to set up a rig location and rig floor more intuitively, finding ways to operate equipment more effectively or creating efficiencies by identifying tools more suitable to a task.
For other great articles about exploration, drilling, completions and production, subscribe to The American Oil & Gas Reporter and bookmark www.aogr.com.