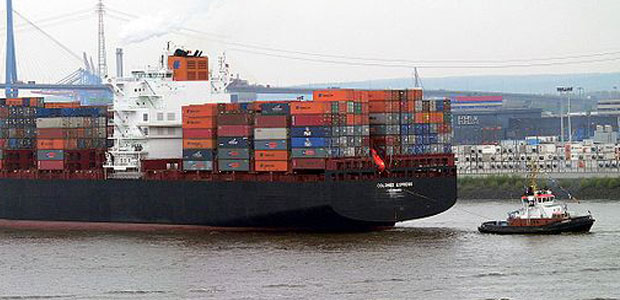
Policies Taking Shape For Natural Gas-Fueled Ships
By Timothy E. Meyers and Lt. Nicholas A. Woessner
WASHINGTON–Air pollution prevention requirements are driving the marine industry to seek advanced technologies to reduce emissions. Many of the emission reduction systems being considered for use on board vessels have been proven in land-based applications, and are being adapted to the marine environment. Following the lead of natural gas vehicles onshore, one such technology is using natural gas as a shipboard fuel to power ocean-going vessels.
As demonstrated in trucks, buses and other NGVs on land, using natural gas as a transportation fuel can provide significant reductions in emissions, compared with diesel. The pricing and availability of natural gas also make it highly competitive from an economic perspective, compared with more traditional marine fuels.
Consequently, natural gas has emerged as a leading alternative for meeting current and future emissions requirements in marine transport, including the limits for emission control areas (ECAs) adopted in amendments to Annex VI of the International Convention for the Prevention of Pollution from Ships (MARPOL). By instituting progressively more stringent limits for oxides of nitrogen and sulfur oxide emissions for the global shipping industry over the next decade, Annex VI is a major motivation for switching to natural gas fuel.
Using natural gas as fuel is one of the most promising methods for meeting these new emission standards. Although natural gas-fueled ships are a relatively new development, liquefied natural gas cargo ships have used cargo boil-off to fuel their propulsion boilers for more than 45 years. More recently, LNG has been used in dual-fuel ship engines. Since 2000, Norway has authorized LNG-fueled ships to operate within its waters, and has acquired significant expertise and experience in designing, constructing, operating and inspecting these vessels.
The U.S. Coast Guard has reviewed several natural gas-fueled vessel concept designs, and has received numerous inquiries from vessel designers, operators and engine manufacturers that are considering using this technology on commercial vessels. Interest in gas-fueled marine applications has spanned a full range of vessel types, including passenger vessels and ferries, offshore supply vessels, container roll-on/roll-off ships, and towing vessels. Several of these concept designs have matured, and their detailed designs have been reviewed by the USCG’s Marine Safety Center. It is expected the U.S. maritime industry will continue to pursue natural gas-fueled vessels as emission limits become stricter over the next several years.
USCG has been reviewing concept proposals for natural gas-powered vessel designs on a case-by-case basis as equivalency requests to requirements under Title 46 of the Code of Federal Regulations (CFR), and it now is offering a streamlined approach to design approval under Policy Letter 01-12.
Emission Limits
Under MARPOL’s Annex VI, progressively more stringent limits for NOx and SOx emissions are being placed on the global shipping industry over the next decade. Within U.S. waters, these requirements are implemented through the Act to Prevent Pollution from Ships (APPS). NOx emission limits are being imposed in a tiered approach, based on engine speed, while SOx is being limited primarily by regulating sulfur content in fuel. Tables 1 and 2 show details of both standards.
The most stringent requirements come into play within ECAs that encompass a 200-nautical-mile band around most of North America and the Hawaiian Islands, and 40-50 nautical miles around Puerto Rico and the U.S. Virgin Islands (Figure 1). Once fully in place, vessels operating within these areas will be subject to the most stringent emission requirements.
Although several technologies are being considered to address these limits (including advanced diesel engine design, exhaust aftertreatment, alternative fuels, and alternative power sources), using natural gas as a fuel is one of the most promising solutions for meeting the new emission standards. By converting from diesel to natural gas, some internal combustion engine manufacturers report reducing NOx as much as 85 percent and eliminating SOx totally, since natural gas does not contain sulfur.
Accordingly, a gas-fueled engine can be compliant with even the strictest emissions requirements, which makes natural gas a seemingly ideal solution for meeting the increasingly stringent air quality mandates, especially for those vessels operating within U.S. ECAs.
The International Maritime Organization (IMO) is expected to finish developing an international code on safety for ships using natural gas and other low-flashpoint fuels (International Gas Fueled Ships Code, IGF) in 2014. The Coast Guard is the primary U.S. representative to the IMO for all policy development, including the continued development of this new code. With the code still under development, it was decided that interim guidance was needed. As a result, in June 2009, the IMO published Resolution MSC.285(86), Interim Guidelines on Safety for Natural Gas-Fueled Engine Installations in Ships.
In addition to the IMO interim guidelines, most of the major classification societies, such as Det Norske Veritas, Germanischer Lloyd, and the American Bureau of Shipping have published rules or guidelines for gas-fueled ships. Each of these classification society standards is closely aligned with the IMO interim guidelines, and in some cases, provides more comprehensive requirements.
Policy Development
The U.S. Coast Guard is continually developing its knowledge, experience and expertise in using natural gas as a marine fuel. The majority of the USCG’s experience is based on developing and applying the International Gas Carrier (IGF) Code to LNG carriers, and the Coast Guard’s own domestic requirements for gas carriers in 46 CFR Part 154.
USCG has been actively involved in developing IMO’s interim guidelines, and the ongoing development of its IGF code. The Coast Guard also has reviewed various class society rules on gas-fueled engine installations, as well as conducted site visits on board gas-fueled vessels to enhance awareness of how the technology is being implemented.
USCG has reviewed and accepted several concept proposals for vessel designs that incorporate natural gas-fueled systems. These concept reviews were conducted on a case-by-case basis so that an equivalent level of safety could be established to the requirements of existing regulations. So far, each of these designs has incorporated the IMO interim guidelines as a base-line standard.
In an effort to streamline the process and provide upfront design criteria, the Coast Guard has published Policy Letter 01-12 to provide one avenue for determining an equivalent level of safety to the CFRs. If a design meets the criteria in the policy, the applicant can skip the concept review process and proceed to the USCG Marine Safety Center for plan review. The policy uses the IMO’s interim guidelines as a base-line standard, and provides additional requirements to ensure an equivalent level of safety.
The policy letter lays out one set of design criteria for demonstrating equivalency, and is very prescriptive in some areas. However, the USCG recognizes there may be other means of achieving equivalency. If a design falls outside the limits of this policy, the applicant still can bring a proposal to headquarters for concept review and design basis approval on a case-by-case basis.
Concept Approval Process
Since U.S. regulations do not address using natural gas as fuel on commercial vessels, a company seeking approval generally submits a request to the Coast Guard’s Office of Design & Engineering Standards for an alternative design under 46 CFR 50.20-30. Successful concept approvals for gas-fueled vessels have included general arrangements, a layout of the gas-fueled system components, and a list of standards proposed for system design. Proposals the Coast Guard has accepted have used the IMO interim guidelines as a base-line standard, and have provided details on how each provision of the interim guidelines would be met and how any deviations were to be addressed.
The USCG’s response to these proposals has taken the form of a design basis agreement that lays the framework of requirements that need to be met for plan approval and vessel certification. So far, this process has proven successful in identifying significant issues early in the design phase, which should avoid having to make major changes in the later stages of design and construction.
Once a design basis agreement has been obtained, a detailed plan review can be conducted by the Coast Guard’s Marine Safety Center (MSC). Procedures for submitting plans can be found in 46 CFR Subpart 50.20. The MSC will conduct a full review of drawings, equipment selection and automation, ensuring that plans are in line with the design basis agreement.
During construction, USCG marine inspectors ensure that a vessel is built according to approved plans. For the construction of a gas-fueled ship, members from the MSC and the Coast Guard’s Liquefied Gas Carrier National Center of Expertise also may accompany local marine inspectors during initial inspection. To avoid unnecessary construction delays, it is crucial that work not be started until plans have been approved.
Training Requirements
Federal, state and local officials have always been concerned with LNG cargo carriers, and now that using natural gas as a fuel is being considered, they would like to ensure that all personnel on board are well versed in its safety, operation and maintenance. Because of this, the Coast Guard is considering documented training requirements to ensure crew members and other personnel have appropriate and sufficient knowledge to operate these vessels safely.
As a starting point, general crew training requirements are outlined in IMO interim guidelines MSC285 (86). There are three categories of training: levels A, B and C. Level A is a basic safety course for all crew members, while level B is an advanced course specifically for deck watch officers, and level C is an advanced course specifically for engineering officers.
This is a risk-based approach. In other words, those directly involved in operating the fuel systems and those responsible for the safety of the ship and crew will receive more extensive training than the basic safety training needed by the remainder of the crew.
In the past, these types of courses have been given by the engine manufacturer, and the crew completion records were held aboard the ship. As a reference, the Norwegian Maritime Directorate (NMD) requires this approach. In addition, NMD requires that owners submit their training plans for approval. This approach has worked for Norway, and the USCG is evaluating whether it will apply in U.S. waters.
The Coast Guard believes that if ship systems are designed properly and crew members are trained adequately, natural gas-fueled ships can be operated safely and efficiently. This requires designing the engineering and control systems using principles derived from human factors as well as safety engineering. Since crew training policy and regulations have not yet been promulgated, requirements will again be considered on a case-by-case basis.
Design Considerations
The following discussion highlights some important issues to be considered in gas-fueled ship design, and provides some insight into USCG’s approach to determining safety equivalency as it pertains to shipboard natural gas-fueled systems. Among the considerations are:
- Fuel system issues (machinery space configurations, fuel tank placement, compressor rooms, and tank and piping requirements);
- Gas detection (system certification);
- Hazardous locations (classification of areas, and electrical equipment selection and certification); and
- Fire protection (installed firefighting systems and fire detection).
The IMO interim guidelines provide two basic design concepts for engineering plant arrangements on natural gas-fueled ships: the inherently gas safe concept, and the emergency shutdown (ESD) concept. Both designs employ safety strategies to mitigate the risks posed by running a natural gas distribution system within a machinery space.
For the inherently gas safe concept, machinery spaces are considered gas-safe under all conditions. This arrangement requires natural gas fuel piping within engine room boundaries to be fitted in a gas-tight enclosure. This is accomplished using double-walled pipe, or single-walled piping within a gas-tight duct. The space between the inner and outer pipe/duct must be either pressurized with inert gas or ventilated.
The machinery space is considered a nonhazardous area, and there are no restrictions on electrical equipment installations. This is very similar to the gas fuel distribution system on LNG carriers that use cargo boil-off as fuel.
For the ESD concept, machinery spaces are considered gas-safe under normal conditions, but have the potential to become gas-dangerous spaces under certain abnormal conditions. This concept allows single-walled piping inside the engine room without an external gas-tight enclosure. Extraction ventilation, at the rate of 30 air changes per hour, is used to prevent the accumulation of flammable vapors within the space. In the event gas is detected at low levels within the space, all electrical equipment not certified safe for hazardous locations is automatically shut down.
The ESD concept was developed when engine manufacturers had not yet engineered a proper solution for fitting double-walled piping to the fuel manifolds on internal combustion engines. With advances in technology, this is no longer an issue for the majority of engine sizes.
A significant element to the ESD concept is that it relies heavily on active safety measures. Specific concerns with this method are that gas detection sensors require careful upkeep and maintenance, and the automation systems that translate sensor signals into alarms and shutdowns contain multiple components that are subject to failure. This concept may require additional maintenance costs and further testing.
Thus far, the systems that have been accepted as meeting an equivalent level of safety to that of existing regulations have been of the inherently gas-safe type.
Fuel Tank Placement
It should be noted that the USCG’s Policy Letter 01-12 does not address fuel stored as compressed natural gas, single-wall gas piping in engine rooms (ESD concept), fuel tanks below accommodation spaces, or portable fuel tanks. There is some debate among IMO members developing the IGF code about placing fuel tanks below accommodation spaces, service spaces, and control stations (Figure 2).
Although the IMO interim guidelines do not prohibit this arrangement, it goes against the long-standing safety practice applied to gas carriers. Specifically, there is a clear separation between LNG storage tanks within the cargo block of the vessel and other areas of the vessel not related to cargo operations. The concern is especially heightened in the case of a vessel carrying passengers.
Design constraints of ship types–other than gas tankers–may not allow a well-defined area between transverse watertight bulkheads to be dedicated exclusively to storing and transferring natural gas. Acknowledging this, the IMO interim guidelines provide several layers of protection to further reduce the risk of fuel system failure, and to mitigate the hazards caused by a leak or rupture in the fuel system. These include gas detection with associated alarms and shutdowns, continuous negative-pressure ventilation of the tank room at 30 air changes per hour, and liquid level and temperature monitoring systems in the tank room bilge.
Additionally, the tank room is considered a zone 1 hazardous space, prohibiting the installation of noncertified electrical equipment. In addition, tank room boundaries must be constructed of cold-resistant material and be thermally insulated from the hull structure. Various class societies have considered additional requirements for tanks under accommodation areas on passenger vessels. These include providing a cofferdam between the tank compartment and adjacent machinery or accommodation space. Also, fuel tanks are placed at a distance of B/5 from the hull, where B is the vessel’s beam.
Tank placement relative to other areas on a gas-fueled ship will require considerable thought. The various risks to the tank and their consequences must be weighed and careful consideration given to the measures taken to prevent or mitigate these consequences.
Compressor, Tank And Piping Standards
U.S. maritime regulations require compressor rooms on chemical and gas carriers to be located above the freeboard deck, with the entrance leading from the weather. Section 3.2.2 of the IMO guidelines also require compressor rooms to be located above the freeboard deck, but there is an allowance for locating them below decks, if they meet the provisions for tank rooms.
Section 2.8.1 of the IMO interim guidelines specifies that an LNG fuel storage tank should be independent and designed in accordance with Chapter 4 of the ICG code. The domestic equivalent of this standard for U.S. vessels is found in 46 CFR §154.401 through §154.476. With regard to recent concept approvals, the Coast Guard has required the use of either this equivalent domestic standard, or alternatively, has allowed type C independent fuel tanks to be designed to the ASME boiler and pressure vessel code Section VIII Division 1 or 2.
In either case, equivalency determinations have been based on the containment system meeting the additional provisions in Section 2.8.1 of the guidelines specific to gas-fueled installations.
In consideration of CNG storage tanks, the IMO interim guidelines do not provide a design standard, but state that they should be approved by the administration. For U.S. vessels, the USCG will consider storage tank designs on a case-by-case basis. The tank should be designed to an established standard suitable for the service intended.
In addition to meeting the provisions of Sections 2.2 and 2.5 of the IMO interim guidelines, piping for natural gas fuel must meet ASME B31.3 process piping standards.
Hazardous Locations
Section 4.3 of the IMO Interim Guidelines uses the International Electrotechnical Commission’s (IEC) zone-based system for classifying hazardous locations, and provides a listing of those spaces and areas on a gas-fueled ship that should be classified as zone 0, zone 1, or zone 2. Over the past several years, the Coast Guard has been transitioning from the division-based system of classification used under the National Electric Code (NEC), to the IEC zone-based system. However, there is not a direct correlation between area classifications under the two regimes.
To be consistent in classifying hazardous areas on a gas-fueled ship in comparison with similar areas on other U.S. vessels, a good starting point is to consider the definitions for “gas safe” and “gas dangerous” spaces given in the gas carrier regulations under 46 CFR 154.7, and the corresponding hazardous area requirements for gas carriers under 46 CFR 111.105-32. While these requirements apply to flammable gas cargoes, and are not divided into zone categories, they do provide insight into how the USCG may classify hazardous areas around similar functional components of a gas-fueled system.
In selecting electrical equipment that may be located in these hazardous areas, the Coast Guard under 46 CFR 111.105 recognizes certification of electrical equipment to either NEC or IEC based standards. Accepted protection techniques are listed in 46 CFR 111.105-9, 11 and 15. Any electrical equipment installed in a hazardous location must comply with one of the standards listed in 46 CFR 111.105, but not combined in a manner that would compromise system integrity or safety.
The regulations in 46 CFR 111.105 further state that the electrical equipment required by these standards to be “tested and approved” must be certified by an independent laboratory recognized by the USCG under 46 CFR 159.010. To date, the Coast Guard has not accepted certification under the European Union’s ATEX directive as proof of having met this requirement.
Gas Detection, Fire Protection
While Section 5.5 of the IMO interim guidelines contains requirements for gas detection on gas-fueled ships, certifying these systems is not addressed. On currently approved gas-fueled vessel concepts, the Coast Guard has required fixed gas detection systems and portable detectors to be listed or certified by an independent laboratory accepted by USCG under 46 CFR Part 159.
Under the IMO interim guidelines, a water spray system must be installed to protect exposed surfaces of a fuel tank, if it is on the weather deck. On currently approved gas-fueled vessel concepts, the Coast Guard has required the boundaries of the superstructures, compressor rooms, pump rooms, cargo control rooms, and any other normally occupied deckhouses that face the storage tank to be protected by a water spray system as well.
The interim guidelines require bunkering stations be protected by a dry-chemical-powder fire extinguishing system. On currently approved gas-fueled vessel concepts, USCG has required such a system to consist of a hand hose line unit that is listed for fire service by a nationally recognized testing laboratory, as defined in 29 CFR 1910.7, and that meets the requirements of 46 CFR 154.1155 and 154.1165-154.1170, as well as the provisions of MSC.1/Circ.1315.
The interim guidelines specify that fire detectors must be provided in tank rooms, ventilation trunks for tank rooms below decks, and machinery spaces containing gas-fueled engines. On currently approved gas-fueled vessel concepts, USCG has required fire detection systems be approved by the Coast Guard in accordance with 46 CFR 161.002 and installed in accordance with 46 CFR 76.27.
Bunkering Considerations
Regarding vessel bunkering, natural gas-fueled vessels may, in concept, receive fuel in a number of ways. Methods used in Norway consist of a direct supply from LNG storage tanks located onshore, where vessels can refuel at their convenience, and using LNG tank trucks that deliver LNG similar to the method used to deliver diesel fuel. Additionally, vessel-to-vessel transfers whereby LNG is offloaded from a barge alongside a vessel also are being considered.
USCG is considering requirements specific to each type of operation and will consider proposals pursuant to the applicable regulations. Owners and operators planning to use natural gas for fuel are encouraged to contact the Coast Guard’s Office of Operating & Environmental Standards, Vessel & Facility Operating Standards Division (CG-OES-2), to discuss project details.
Using natural gas as fuel is a promising technology for complying with upcoming emission limits. It is hoped that ship owners and designers will benefit from reviewing these considerations when developing conceptual designs for gas-fueled ships, and it is highly recommended that they start discussions with the USCG early in the design process.
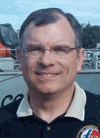
Timothy E. Meyers is a general engineer in the U.S. Coast Guard’s Office of Design & Engineering Standards, Systems Engineering Division, in Washington. His primary focus is on U.S. policy and standards for commercial vessel systems using alternative fuels, and the shipboard classification of hazardous locations. Meyers is the USCG’s lead engineer engaged in regulatory and policy development for the safe design and engineering of natural gas-fueled vessel systems, and represents the United States on the International Maritime Organization’s Correspondence Group for developing the International Code of Safety for Ships Using Gases or Other Low-Flashpoint Fuels (IGF code). He has 22 years of experience with USCG in enforcing, interpreting and developing U.S. and international maritime safety and security regulations. Meyers holds a bachelor’s in applied science from the U.S. Coast Guard Academy and a master’s in chemical engineering from the University of Virginia.
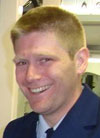
Lt. Nicholas A. Woessner is a marine engineer at the U.S. Coast Guard’s Marine Safety Center. He has been involved in developing the USCG’s policy for natural gas-fueled vessels, and has conducted multiple concept and detailed design reviews of natural gas-fueled vessels. He has seven years of service in the USCG, including three years in the marine safety field. Lt. Woessner holds a bachelor’s in naval architecture and marine engineering from the U.S. Coast Guard Academy, and a master’s in naval architecture and marine engineering and industrial operations engineering from the University of Michigan.
For other great articles about exploration, drilling, completions and production, subscribe to The American Oil & Gas Reporter and bookmark www.aogr.com.