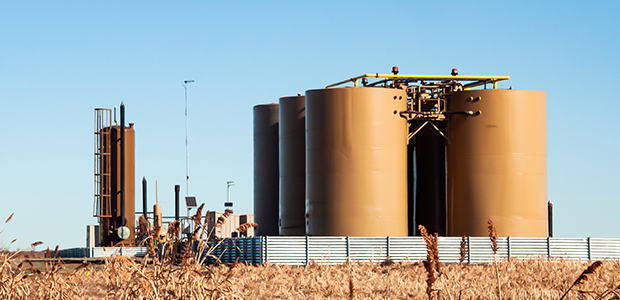
Pressure Sensors Illuminate Path To Lower-Cost Vapor Recovery
By Mark V. Goloby
Vapor recovery units have a long history of capturing vapors from tank batteries that otherwise would vent to atmosphere. Whether these vapors are sent to a sales line or flare, eliminating them helps operators reduce emissions and maintain regulatory compliance.
When the VRU connects to a sales line, the extra revenue can pay for the VRU quickly and increase profits or at least minimize the cost of regulatory compliance. After all, the vapors from production tanks tend to be high BTU and therefore high value. The more the VRU collects, the more attractive the economics. For this reason, installing VRUs on tank batteries that see considerable production is easy to justify.
We are conducting research aimed at improving VRU economics in low volume, low pressure applications. Collecting data on how various field conditions affect tanks’ internal vapor pressures, this research may reduce the time required to identify the right VRU for a specific application. Ultimately, the goal is to develop a standardized design that can achieve economies of scale and reduce costs. Readily-available information about a facility’s design, environment and production characteristics that we are trying to correlate with changes in tanks’ internal pressure dynamics include:
- Ambient temperatures;
- Fluid levels within the tank, which influence air space pressure between the fluid and top of the tank;
- Fluid temperature; and
- Production process equipment, including separators, heater-treaters and dehumidifiers.
To reveal correlations between these factors and internal pressures, we have partnered with several producers in Texas and throughout the Mid-Continent to temporarily install wireless pressure sensors inside tanks. These sensors use low-pressure transducers capable of detecting changes below 1 psi, enabling them to provide a unique perspective that links field activities and ambient conditions to shifts in internal tank pressures.
If this data merely confirmed what engineers already knew, it would no longer be worth collecting. But as two recent installations illustrate, the sensors’ findings often prove interesting.
Morning Pressure Spikes
The first of those installations measured vapor pressures across several months. Suddenly, tank pressures began increasing every morning. After verifying that field operations were proceeding normally, we considered an obvious explanation: The rising sun heated the tank and caused the vapors inside to expand. The data was collected during a summer in which Texas experienced a significant heat wave, so the temperatures were impressive.
To inform development of vapor recovery units for low-volume, low-pressure applications, an ongoing research project is installing wireless pressure sensors in production tanks. At this site, the sensors revealed that pressure jumped in the morning as rising temperatures released vapors that condensed overnight.
Even so, the explanation did not fit the data. If the sun were the cause, pressures should have begun increasing in the morning and remained elevated or even continued to grow until the sun reached its zenith. Instead, the pressure spike only lasted 90-120 minutes.
With field technicians reporting nothing of note operationally, the quest for a satisfying explanation initially proved baffling. But further investigation yielded a plausible explanation. As the tanks cooled at night, the vapors inside condensed into liquids. Even a tiny temperature increase—like the one that invariably occurred in the morning—would cause the liquids to come out of suspension in a gaseous state, creating the sudden increase in internal vapor pressure.
The tank level influenced the pressure spike’s duration. The fuller the tank, the faster the vapors would be released from other outlets.
The fact that vapors get into solution at night and then come out of solution during the day can reduce the frequency at which the VRU needs to capture the vapors. Since we are trying to power the VRU with solar panels, using power efficiently is essential.
Springs’ Role
The second case that illustrates the wireless pressure sensors’ value occurred at a site where we were already monitoring wellhead tubing pressure and tank levels. With all the data going into a common database, it was much easier to compare data, and we could document the correlation between surges in tubing pressure and increases in tank pressure with greater precision.
More interesting was tank levels’ minimal impact on internal vapor pressure. As the tank level rises and the void space between the fluid and the top of the tank shrinks, pressures should climb. That may have happened, but the tank hatches were equipped with only four-ounce springs, which meant the hatches opened once pressures exceeded four ounces and released the excess pressure before it could be quantified. These unquantified pressure increases did not happen on the previously mentioned site, where the hatches had eight-ounce springs.
While monitoring the location’s tank pressures, we noticed a sudden pressure jump after the customer’s well went from free flow to artificial lift that utilized a compressor. This observation suggests that thief hatches should be opened as an enhanced safety precaution during compressor installation or other major facility reconfigurations. Whether that is necessary will depend on the facility’s configuration.
The sensors have documented notable spikes in pressure when wells move from free flow to compressor-based artificial lift. As an extra safety precaution, it may be worthwhile to open thief hatches during compressor installation or other facility reconfigurations that are likely to increase pressures.
One very important aspect the data illustrates is the critical role hatch seals and hatch spring strength play in vapor recovery management. Before installing a VRU, operators should ensure the seals are in good condition and the hatch spring strength is appropriate. In most applications, we recommend using eight to 10-ounce springs; these should allow the VRU to better capture expected vapors by preventing the thief hatch from opening unnecessarily, but enable it to open in the event of dangerous pressures.
We continue to seek partners who will let us gather tank vapor pressure readings to better understand vapors’ behavior in common facility configurations. This research should make it easier to deploy VRUs at a cost low enough to be economic even for tanks with limited production. Coupled with improvements to complementary technologies, including solar panels and hatch seals, more affordable VRUs should enable operators to boost revenue while limiting emissions.
Editor’s Note: This article is a follow-up to May 2021’s Study Gathers Data on Oil Tank Vapor Pressures, which describes the wireless sensors in greater detail. The author would like to thank William Shelton, P.E., for his assistance in developing this update.
MARK V. GOLOBY is president of TC Technologies, which is involved in a variety of initiatives to deliver wireless monitoring tools for oil and gas production and related assets. Goloby has more than two decades of experience implementing cost-effective wireless data solutions. He was previously with Mertrix Networks and is a graduate of Texas A&M University.
For other great articles about exploration, drilling, completions and production, subscribe to The American Oil & Gas Reporter and bookmark www.aogr.com.