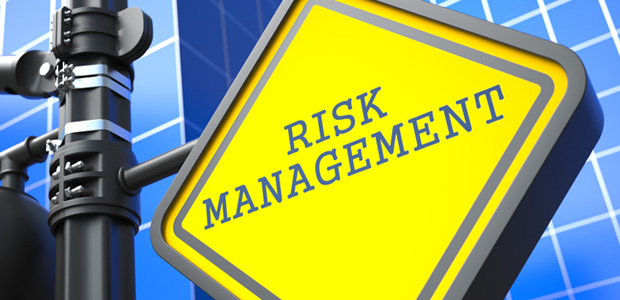
Risk Management
‘Safety Culture’ Key To Business Success
By Davide Vassallo, Mieke Jacobs and Sebastien Planche
PHILADELPHIA–The industry has experienced turbulent times during the past few years. Faced with low commodity prices and global oversupply of crude oil, many oil producers were forced to react by introducing drastic cost-cutting measures to readjust cost structures.
While business conditions are improving, it has become apparent that volatility in crude oil prices occurring in ever shorter cycles now is likely the “new normal” for the industry. Oil producers need to become more agile in adjusting to price movements if they want to remain profitable. Historically, the impact of cost-cutting exercises in response to falling prices is generally slow to take effect. Like a ship whose engine has just been stopped, companies continue to be carried forward by their existing momentum, requiring many months to fully adjust operating expenditures and operating portfolios.
Past experience also shows that a rise in the frequency of lost time injuries occurs in the industry about two years after a drop in oil prices. So more than two years after prices collapsed and the industry began shifting its focus to cost control measures, many now face the question of how to adjust their safety roadmaps and risk mitigation processes to protect the business efforts that deliver cash from their operations.
It is during times of price instability that operational risk management–identifying, evaluating and controlling hazards based on potential levels of severity and the likelihood of occurrence–should remain a top priority for oil and gas companies. Taking such steps will enable them to avoid costly incidents and high insurance premiums while continuing to drive profitability, ensure worker safety, and maintain future operating capabilities.
Operators are hopeful that a recovery now underway, particularly in U.S. unconventional resource plays, but commodity price uncertainties require companies to continue on the journey of tightly controlling capital expenditures and optimizing operational efficiencies.
What risk management lessons does the industry’s past teach about its near-term future? As Figure 1 illustrates, after oil prices dropped from 2000 to 2002, a 6 percent rise in lost time injury frequency followed in 2002-03 as activity began bouncing back. And again, after oil prices fell sharply in 2008-09, the industry experienced a 14 percent increase in lost time injury frequency rates in 2012 compared to the levels recorded in 2010.
Real Dilemma
There are multiple reasons for these increases in safety incidents, but the risks represent a real dilemma for the oil and gas industry. Companies would be wise to take urgent action now to address all the potential risks and avoid problems as the market picks up again. To mitigate the risk of future safety incidents, operators and service and supply companies cannot afford to wait until the market is in full recovery mode.
One thing companies can do to improve operational risk management during downtimes is to ensure that a strong culture of safety exists among workers. A necessary first step to achieving this goal is to understand the current organizational safety culture. While companies have generally experienced good safety performance during times when crude oil prices are high, the industry as a whole operates in a fairly rigid and rules-driven culture. In other words, it is a “dependent” culture in which employees perform risk management activities because of strict requirements, including both company rules and government regulations.
The industry would benefit by moving toward a more “independent” culture that encourages and expects all employees (and thereby the entire organization) to consciously and regularly make the right, safe decisions in often complex and fast-changing work environments. Such a culture also would allow companies to adapt more quickly to ever-shorter price cycles as the organization becomes more self-reliant and no longer dependent on a few supervisors for safety guidance. Such an evolution would translate into more reliable, sustainable safety performance as well as increased productivity.
However, many oil companies can be unaware of their cultural weaknesses, focusing their attention on other core business issues. That leaves them exposed to exponential dangers since they do not know what hidden risks may be lurking in a stretched organization. The key issues are ensuring that all staff members are motivated and engaged in safety, and that cost-cutting measures have not inadvertently weakened risk mitigation efforts.
Measuring Safety Risks
Safety managers need to be able to measure their organization’s safety culture to effectively and efficiently allocate resources. One tool to determine relatively quickly what areas need urgent attention is a professional safety perception survey of employees. In the oil and gas industry, it is important for this survey to focus on staff working directly at asset sites where there is immediate risk exposure and where operations can react quickly to any hazards identified. If carried out correctly, these results provide a barometer of the prevailing safety culture and help management direct efforts at the right targets.
Safety perception surveys and staff health, safety and environmental assessments are a crucial element in transforming an organization’s safety culture. The findings allow companies to take a differentiated approach to risk and focus on the top threats along the entire value chain (Figure 2). This is an effective approach to identifying hidden areas of risk in today’s oil and gas industry operating climate.
The results of a well-conducted employee safety survey make it possible to differentiate between short-term risk containment and long-term sustainable risk reduction goals. Often, a roadmap of activities to enable an organization to implement critical actions can be developed in a few as 90 days.
In a business where all expenditures have to be highly effective, it is critical that safety efforts are determined by an alert approach and executed by a cohesive, independent culture. Learning to be agile now will benefit companies in the future. Flexibility in reducing production, operating and capital expenditures when the price of oil is low without increasing risk will become ever more critical, and allow companies to react more quickly when oil prices rise. Although this may seem a tall order, it is definitely achievable with the right tools to identify and prioritize risks.
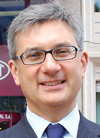
DAVIDE VASSALLO is global managing director of DuPont Sustainable Solutions. Since joining the company in 2010, Vassallo has focused on helping corporations improve efficiency and business performance while reducing their environmental footprints. He holds a degree in environmental engineering from the Polytechnic of Turin, Italy.
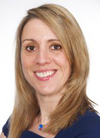
MIEKE JACOBS is a senior consultant to DuPont Sustainable Solutions. Since joining DuPont in 2000, she has held positions focused on supply chain management and safety. Jacobs holds master’s degrees in commercial engineering and economics.
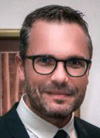
SEBASTIEN PLANCHE is a senior consultant to DuPont Sustainable Solutions and president of PerfWell Advisory. With two decades of industry experience, he previously served in management positions at Schlumberger, Hitachi Consulting and Shell. Planche holds master’s degrees in technology and management, financial management, and economics.
For other great articles about exploration, drilling, completions and production, subscribe to The American Oil & Gas Reporter and bookmark www.aogr.com.