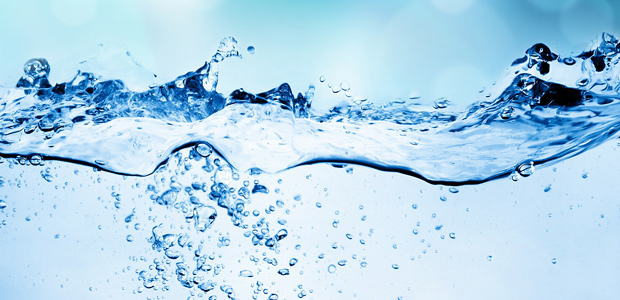
Water Management
Water Recycling Enhances Well Economics
By Ed Candia and Kushal Seth
HOUSTON–Producers are looking for new technologies and techniques to lower operating costs and improve performance in tight oil and shale gas plays in an effort to navigate the down cycle in commodity prices. One solution that has interested producers both large and small is the practice of recycling produced and flowback water for reuse in hydraulic fracturing operations.
Water recycling is quickly becoming a best practice for operating companies active in shale plays from the Marcellus and Utica in the Northeast, to the Eagle Ford and Permian Basin in Texas, to the Niobrara in Colorado and Wyoming. By recovering and reusing flowback and produced water, operators can eliminate the need to access and transport millions of gallons of freshwater to each well location, while also minimizing disposal-related costs after the well is hydraulically fractured and placed on production.
“With both oil and gas prices down right now, it is critical that operators are mindful of every penny they are spending,” says Jim Doré, an industry consultant with Beyond Consulting LLC. “The lower the drilling, completion and lifting costs, the better the well economics. Recycling water is not only good for the environment, but it saves transportation costs, disposal fees, and significantly reduces the amount of spent water going into injection wells.”
It all comes down to the economics. Water management has become such a critical part of onshore well stimulation and completion processes that it cannot be ignored. On an average shale well, operators can save anywhere from $50,000 to $300,000 by using advanced technology to recycle their water.
And as something of a bonus to the operator, the oil recovered from the recycling process can be returned to the operator. Even if only 0.1 volume/volume (V/V) percent of oil is recovered from produced water or flowback fluids, it can provide a substantial savings, sometimes even generating enough money to pay for the water recycling operation itself. The amount of oil recovery depends on the well, but there have been instances where up to 2 percent V/V of oil was recovered from the water stream.
Given the economic incentive and the continuing evolution of treatment technologies, oil and gas companies are leveraging a range of water management strategies and treatment methods in their operations. The growing demand for recycling solutions has given rise to many small regional companies, but it has also caught the attention of some of the largest and most established names in the oil field services sector.
Many service companies are using legacy technology that has been in place for years, such as belt filter presses (originally designed to clean up holding ponds at drill sites) or gravity filtration. Some of the more established companies have developed their own proprietary legacy equipment designed to produce more clean water for field use purposes.
Multifaceted Approach
Advanced water recycling equipment and technologies can remove up to 99.9 percent of certain contaminants from produced water and flowback streams while achieving high treatment efficiencies and small operational footprints.
From the operator’s perspective, however, the best strategy is to take a multifaceted approach to water treatment, utilizing a menu of technologies depending on the specifics of the application and the treatment requirements. Just as no two shale wells are exactly the alike, neither are the waters they yield during the flowback and production phases, making a “one solution fits all” approach ineffective.
The advent of unconventional resource plays has made water management an increasingly important part of onshore operations, but it has long been integral to offshore drilling, completion and production. The offshore environment not only has stringent treatment and discharge standards, but also has equipment size and weight constraints given space limitations on offshore facilities. Drawing on decades of experience in both subsea and surface separation and treatment, the lessons learned offshore can now be applied to optimize treating and recycling operations onshore.
The result is compact, lightweight recycling technologies with the capability to remove up to 99.9 percent of certain contaminants from both produced and flowback water. Smaller operational footprints on the pad site and the portability to easily move from one multiwell pad to another are key, as are low maintenance requirements and the ability to achieve high pretreatment and treatment efficiencies.
With highly portable and efficient equipment components, multiple treatment methods can be integrated into a single “total solution” system designed to meet the particular needs of a given pad or drilling campaign. The first step in the process is generally a cyclonic de-silter derived from technology originally developed for subsea processing that removes particulates down to 10 microns in diameter with greater than 95 percent efficiency.
Depending on treatment requirements, the next steps can include a high-efficiency biocide, electro-coagulation, cyclonic floatation, and silicon carbide ultrafiltration membranes for advanced custom treatment. These applied technologies can reduce components such as boron, iron, oil and grease, and bacteria by 99.9 percent.
The advantages of using cyclonic technology are not only cleaner water, but also less time needed to treat it. Traditional legacy technologies using gravity take time, which equates to dollars lost while waiting for treatment. A cyclonic de-silter processes water significantly faster, meaning less downtime at the production site, and in turn, more money to the operator’s bottom-line.
Moreover, the technology’s heritage in subsea operations means it has been developed to be highly reliable as well as lightweight, compact and quick-to-move. If an operator in a shale play is looking for water treatment on many wells in a concentrated area, the equipment can be set up in only a few hours. Once a job is complete, the system can be dismantled just as quickly and transported to another well location.
Win/Win Solution
With a water recovery rate between 90 and 98 percent, depending on the quality of the treated volume, the cost savings that come from using these advanced technologies is significant. Reusing produced and flowback water means lower freshwater usage, trucking and storage, and the cumulative cost savings associated with those activities only increase when treating water from multiple wells on a pad or multiple pads in a field area.
Water recycling also means less water transport trucks on the road, which means less risk for a traffic incident, less road repairs and less truck noise for communities where hydraulic fracturing and conventional drilling are taking place, creating a win/win situation for all parties.
Compact, portable treatment solutions are ideal for unconventional resource plays because they can be set up and dismantled quickly, and are easily transported from one pad location to another. Shown here is a compact inline dewaterer that was developed to recover oil from produced water and flowback in shale plays.
The U.S. Environmental Protection Agency estimates that it takes between 70 billion and 140 billion gallons of freshwater to fracture 35,000 wells a year. That equates to the amount of water that is used by the city of Houston in an entire year. So it is easy to see why recycling water is important if America is going to stay on the road to energy independence.
It also explains why water treatment and recycling is one of the fastest growing sectors within the energy industry, as detailed in a recent Wall Street Journal article. Already a multibillion-dollar business, the prospects for growth are predicted to continue even with depressed oil prices, although there will be some stumbling blocks along the way.
One issue facing operators dealing with flowback is making sure that potential hydrogen sulfide is removed from the flowback before purification and treatment begins. While oil field fatality incidents caused by H2S poisoning from untreated flowback are extremely low, sour gas nevertheless poses serious risk to on-site personnel. The key is using equipment for pretreatment to neutralize hydrogen sulfide while still in solution in the flowback stream, virtually eliminating any risk of H2S exposure during treatment operations after the water has been separated.
Whether H2S pretreatment, disinfection, core treatment or comprehensive customized water treatment using truck- or trailer-mounted equipment at the production site, the ability to select from an array of services and options based on the specific needs of an operation gives oil and gas companies the ability to optimize treatment effectiveness, safety and efficiency.
The net results are cost savings for the operator, and ultimately, improved economic performance in the prevailing low-price environment. One major piece of the “efficiency pie” in shale oil and gas plays is controlling and reducing the costs associated with the massive amounts of water needed. That can be accomplished, at least partly, by having a consistent and well planned water treatment and recycling system in place.
If operators implement effective water treatment strategies today when prices per barrel are low, they will be that much farther ahead of the profitability curve when prices return to normal levels.
Ed Candia is director of flow treatment for FMC Technologies. He has more than 37 years of oil and gas industry experience and has focused his professional activities in directional drilling, business development, administration of foreign investments, oil field operations, supply contracts, and technology enterprises. In his current assignment, Candia is focused on implementing innovative oil, gas, water and solids separation technologies for the unconventional shale market. Candia holds a master’s in international management from the American Graduate School of International Management.
Kushal Seth is the application manager for flow treatment solutions at FMC Technologies. He has more than eight years of experience in oil field water treatment, separation technologies, hydraulic fracturing, production chemistry, flow assurance and operations support. Prior to FMC Technologies, Seth was the application team lead for the water management group at Baker Hughes. He holds more than 10 patents in water treatment, hydrogen sulfide remediation, sulfate removal, corrosion inhibition and well stimulation.
For other great articles about exploration, drilling, completions and production, subscribe to The American Oil & Gas Reporter and bookmark www.aogr.com.