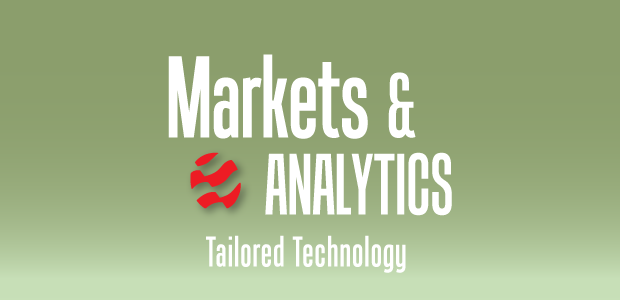
Skill, Attention To Detail A Must For Fitting Together The Permian Projects Puzzle
By Shankar Annamalai
MIDLAND—For a century, the Permian Basin has redefined itself continuously, and in so doing, has played a defining role in progressively shaping the state of the art in oil field technology—from exploration sciences to horizontal drilling and enhanced recovery methods.
A massive endowment of reserves in distinct geological sub-basins with multiple benches in various-aged formations stacked one atop another have generated a seemingly endless list of plays, beginning with shallow sandstones and moving successively deeper to the Cambrian near the bottom of the stratigraphic column. As it turns out, the source rock shales in between, which had been drilled through for decades, hold the biggest reserve prize: tens of billions of barrels of oil and hundreds of trillions of cubic feet of natural gas.
To comprehend precisely how remarkable the past 10 of the Permian’s 100 years of oil production have been, imagine that the shale boom had not happened: Current output likely would be in the range of 500,000 barrels a day. Instead, after years of declines, oil volumes began to trend upward in 2010, exponentially growing to approximately 5.7 million barrels a day today and with predictions suggesting production may top 7 MMbbl/d day in the next decade.
There’s a reason for that: technology.
In particular, the technology to extract hydrocarbons at high rates from ultralow-permeability reservoirs has elevated Permian oil and gas production to all-time records and solidified the region’s standing as one of the world’s foremost supply hubs. Maintaining that position requires innovation and technology deployment similar to that which put the Wolfcamp, Spraberry, Bone Spring and other resource plays on the map in the first place.
There is no single silver bullet. Getting the most out of every dollar invested in every well requires an entire arsenal of options. That is why it is critical for operators to partner with a solutions provider specializing in the full well production life cycle and offering technologies spanning all forms of artificial lift, chemistry, digital automation and optimization, and emissions management. It starts with intelligent chemical treatment of the reservoir during hydraulic fracturing. It requires designing the right lift system, production chemical program and well site control architecture for early-stage production. But once a well comes on line, producers can pull any number of levers to manage the decline curve and maximize production.
The key to knowing exactly which levers to pull, and when, is giving operators access to solutions across the entire production spectrum, along with the subject matter expertise and production-specific experience to fully leverage them to optimize performance over the life of the well.
Purpose-Fit Solutions
Working alongside operators, service companies such as ChampionX have been at the forefront of developing purpose-fit technologies to optimize production from unconventional formations. However, as Permian tight oil plays enter a new phase of development focused on infill locations and areas outside Tier 1 core acreage, the production challenges operators encounter are likely to grow more pronounced and difficult to manage.
That makes innovation and collaboration as important as ever to increasing both well productivities and long-term recovery rates. The good news is that, similar to how advancements in horizontal drilling and multistage completion techniques have revolutionized the way Permian operators construct wells, production technologies likewise are now transforming how they produce those assets.
One of the hard lessons shale plays repeatedly teach is that every well is unique, with its own “fingerprint” of geologic, geomechanical, petrophysical and reservoir chemistry attributes. What works on one well may not necessarily work on another. This heterogeneity, even among laterals sharing the same pad, requires in-depth application expertise to identify appropriate solutions on a well-by-well basis. To efficiently extract more oil in less time, operators need the right technology, experience base and technical knowledge to understand a litany of downhole variables and conditions, and how they can influence hydrocarbon recovery in a highly dynamic environment.
Digital technology is a powerful enabler in getting more reserves out of the ground in less time and at lower cost while unlocking other benefits, such as mitigating operational risk and managing emissions. To be effective, however, digital technology must deliver data science solutions within the framework of production engineering and real-world physical models.
The need for purpose-fit technology and expertise extends into the emissions and decarbonization space. The energy market is evolving, and success is no longer measured in dollars and cents alone. Emissions reduction is also part of the calculation, driving expanded demand for emissions measurement and monitoring using optical gas imaging cameras, continuous monitoring devices, drones, helicopters and aerial surveys.
So how can Permian operators put together all the pieces of the production puzzle to help offset the challenges—increasing water cuts and solids contents, higher gas fractions, more complex wells with longer laterals, environmental and ESG drivers, workforce constraints amplified by retirements, and capital budget pressures, to name a few—and optimize production across the entire portfolio?
Production Expertise
The answer begins with the automation and optimization piece. One of the fundamental rationales for digital technology is the ability to acquire and analyze data to inform decision-making routines—whether using human or artificial intelligence. It’s true that any decision output is only as good as the information input. However, it is equally true that it’s impossible to consistently arrive at correct conclusions or sound corrective responses without adequate knowledge to understand the data and properly translate it into actionable intelligence.
In keeping, having production-specific experience and expertise are as important as having accurate and high-quality data. To be effective, digital technology must be integrated with relevant technical knowledge and relational experiences to make sense of data. In other words, the data science must meet in the middle with production science to deliver data within the framework of production engineering rigors and real-world physical models.
Deploying expert logic diagnostic software with downhole sensors, Internet of Things surface devices, and automation hardware makes it possible for operators to get more reserves out of the ground in less time and at lower cost. Digital automation tools also unlock other benefits, such as mitigating risk and emissions impacts by reducing lease site trips to check well status or make setpoint adjustments. Chemical treatment programs offer another case in point. Automated control of on-site chemical injection pumps and digital dispatching solutions for treater trucks improve treatment efficiency while ensuring the right amount of chemical is delivered when needed.
The state of the art in automation is cloud-based expert logic software that analyzes real-time data using historical correlations to optimize well site operations from pump speed to rod rotation and motor idling. The diagnostic software, controller hardware and sensors work in concert and provide the facility-level control to monitor, measure, diagnose, predict, recommend expert prescriptive actions and sustain operations within preset parameters.
The next evolutionary leap in digital technology is intelligent automation using machine learning and artificial intelligence algorithms embedded within edge devices at the well site for fully autonomous well operations. These leading-edge digital capabilities, tightly integrated with deep domain expertise, are positioned to help truly deliver on intelligent automation’s promise of improving production and equipment uptime using multiple forms of artificial lift.
Higher Rates, Faster Declines
Outside the digital realm, mechanical lift and chemical technologies also are supporting increased well productivities. Propelled by extended lateral lengths with greater intervals of stimulated rock, per-well production from new Permian completions jumped more than 700 barrels of oil equivalent a day between 2010 and 2022, according to Rystad Energy research. For the first time in the Permian’s long history, new wells collectively average more than 1,000 boe/d. At the same time, however, production data implies that aggregate decline rates are accelerating, with higher initial rates falling off faster.
The physics and the geology are always going to win. Every well will start to decline from the moment it commences production. A service company’s job as the operator’s production partner is to get the maximum number of barrels to surface in the minimum amount of time. That again emphasizes the importance of using the correct mechanical lift, chemical treatment and digital controls to raise the decline curve slope as high as possible for as long as possible. It also requires providing equipment with the lowest mean time between failure and chemical treatments to prevent such failures.
Electrical submersible pumping technology is rising to the challenges of Permian tight oil plays with a new generation of compact motors and pumps that achieve greater lift capacities with improved gas and solids handling capabilities in smaller-footprint packages. These solutions also are extending ESPs’ application range with the ability to operate efficiently at rates as low as 200-300 bbl/d.
With today’s high-rate horizontal wells, produced fluids now are moving at such velocities that operators must consider the sheer of chemistries and how the serviceability of a lift system designed to efficiently accommodate 1,000 bbl/d can be maintained as daily rates drop. At the same time, slim hole casing designs are becoming standard, and plays such as those in the southern Delaware Basin are producing high gas-to-oil ratio flows with significant amounts of water and sand.
It is not easy keeping pace with the ever-changing profiles of existing producing wells and the rapidly evolving demands of new wells, especially when business, economic and ESG considerations are layered into the picture. Rather than a fixed menu, Permian plays call for more of an à la carte approach, where the operator can select from various options according to its objectives and well-specific needs. The combination of gas lift and plunger lift may be ideal on one pad, but electrical submersible pumping followed by rod lift may make more sense on the next pad. Integrating all available lift solutions with specialized chemical treatment, digital control and emissions management creates true life-of-well optionality to optimize operations at every stage in the production cycle.
Consider ESP as an example. A new generation of compact ESP motors and pumps are achieving greater lift capacities with improved gas and solids handling capabilities in smaller outside diameter packages engineered for tighter clearances inside the 5.5-inch casing common in Permian unconventional plays. The smaller OD leaves more annular space to slow fluid speed, which reduces gas interference effects and gives these smaller-footprint systems a broader application envelope with the ability to operate efficiently at rates as low as 200-300 bbl/d—territory that until recently was well outside an ESP’s range.
Similar technical advancements are occurring across every form of lift, from algorithms continuously optimizing gas lift injection rates to new plunger designs that can produce as much as 500 bbl/d and rod pumps that lift sand-laden fluids with relative ease. Regardless of type, all lift systems are being plugged seamlessly into a 360-degree digital platform to monitor and optimize performance, and diagnose potential red flags that may escalate into downtime events if they remain unchecked.
Thanks to digital software and sensing devices, emissions information also is being incorporated into production decisions. Emissions management data has become a part of the real-time information flows that operators use to evaluate all available production scenarios to help them select the option with the most favorable outcome. Providing emissions solutions to support producers in collecting and delivering emissions data boosts confidence in the Permian, which is held to high standards of developing sustainable energy.
Partnering with a solutions provider specializing in the full well production life cycle and offering technologies spanning all forms of artificial lift, chemistry, digital automation and optimization, and emissions management is critical to helping operators get the most out of every dollar invested in every well at all points along the decline curve.
With production chemistries, innovative solutions encompass everything from nanoparticles that extend the release of inhibitors to qualified fluids engineered for specific metallurgies and lift types, and flow improvers to lighten the fluid column and enhance gas lift capacity. Advancements to better deliver chemical down hole include highly mobile thru-tubing capillary systems that place treatments at the precise depths in the well where they are most effective and automated injection skids that proportionally meter highly accurate dosages to multiple wells without risk of over- or undertreating.
Oil and gas companies are searching for technologies with impact to produce more with less—fewer people, less capital, fewer workovers, downsized operational footprints, fewer well site visits, etc. Drawing on in-depth subject matter expertise, a great service company’s mission is to responsively deliver cohesive integrated solutions to enable operators to attain these objectives. But it requires fostering a culture that breeds entrepreneurialism and innovation across technical domains and product lines, and promotes external collaboration with operators to solve even the toughest problems.
In some cases, operators may ask their service partners to do things that have not been done before using a mechanical, chemical, digital or emissions solution, or perhaps all the above at the same time. Accomplishing what has never been done before is what has led Permian production to new historic inflection points. The industry will continue to rise to the challenge and innovate to turn what may be unachievable today into standard practice in the next era of Permian unconventional production.
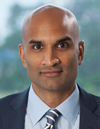
SHANKAR ANNAMALAI is vice president of the Permian Basin geomarket at ChampionX. He joined the company in 2017 as senior vice president of operations at Apergy, which merged in 2020 with Nalco Champion upstream chemicals to create ChampionX, a global provider of artificial lift, chemistry, automation and optimization, drilling, and emissions management solutions. Annamalai previously held a variety of international executive leadership roles with Pentair, including vice president of operations and supply. He holds a B.S. in mechanical engineering and an MBA from Texas A&M University.
For other great articles about exploration, drilling, completions and production, subscribe to The American Oil & Gas Reporter and bookmark www.aogr.com.