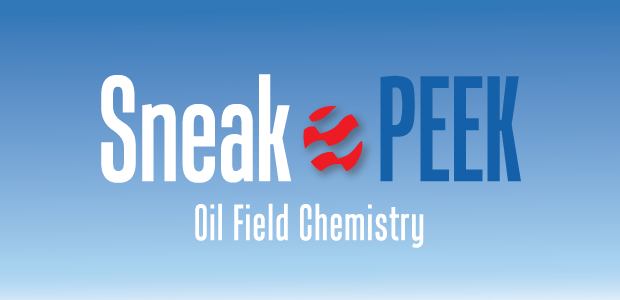
Experimentation Reveals More Effective Chemistries And Deployment Techniques
By Colter Cookson
When construction forces drivers to take detours, they occasionally enjoy the new route more than the old. Today’s oil field chemists are navigating around roadblocks, too. In the process, they are testing novel solutions to longstanding problems and finding more efficient ways to deliver proven chemistries to problematic zones.
That innovation is driven in part by supply chain disruptions. “The raw components used to manufacture chemicals frequently come from outside the United States, so chemical costs go up with shipping costs,” observes Justin Disney, director of laboratory and research and development services for Jacam Catalyst. “With cargo rates five-10 times higher today than they were two years ago and trucking costs rising, many traditional chemistries have become expensive or scarce.”
In the long run, Disney predicts the supply chain disruptions will have a silver lining. “When the industry no longer can get tried and true chemistries in the necessary quantities, people start looking for other ways to solve the same problem. That search is accelerating innovation 10-20 years,” he assesses. “As people try alternatives in applications and quantities they never would have considered previously, they are discovering situations in which the alternatives work better.”
Disney points to the example of hydrogen sulfide scavenging. Because it has become so challenging to obtain MEA triazine, the industry is vetting alternative chemistries. “In natural gas pipeline applications where the scavenger is atomized into the gas, several emerging chemistries seem to be more effective than MEA triazine,” he reports.
Once the global supply chain disruptions ease, Disney predicts most traditional chemistries will come back into favor. “These chemistries have many manufacturers and distributors throughout the United States, which has driven efficiencies that reduce costs,” he explains.
To prepare for future supply chain disruptions, Disney urges chemical suppliers and their clients to continue investigating alternatives. “Given how much supply chain costs can affect price and availability, we cannot afford to be one-trick ponies for a specific problem or application,” he argues. “We need a variety of effective chemistries that we can produce with different precursors. Ideally, these precursors should come from multiple industries so we can shift our supply base in the event of a hiccup in one industry.”
Testing’s Importance
Developing a more resilient supply chain will require help from operators who are willing to try novel chemistries, Disney notes. “If chemical suppliers want operators to do that, we have to anticipate their questions and do enough laboratory testing to address concerns and validate the new chemistry’s benefits,” he says. “We also need to be upfront about what we can reasonably predict from lab tests and any remaining unknowns.”
As global supply chain disruptions have increased prices for and limited availability of traditional chemistries, chemical suppliers and operators have begun testing alternatives on a large scale. According to Jacam Catalyst, a few of these alternatives are delivering such strong performance that they may become the chemistry of choice in specific applications.
Disney says local laboratories can be a powerful aid to innovation. While that is partly because it’s faster and less expensive to send samples to nearby labs, there are other benefits. “We can tell people, ‘Our lab is 10 minutes down the road from your office. Why not come by and watch some of the tests?’” Disney says. “When operators know the people who perform the tests and have seen the equipment we use, they have a higher level of trust.”
Over the past several years, Disney says operators have taken a much greater interest in the science behind chemistry. “They not only want to know what chemistry we recommend, but why we selected it and the testing we performed to confirm it is the right product and to identify the right concentration. In other words, they want to make sure they are solving problems without overtreating.”
Once the chemistry is in the field, Jacam Catalyst uses chemical residual tests, corrosion coupons and other tools to determine if the concentrations have been optimized fully and to spot leading indicators of potential problems. Disney mentions that customers increasingly want chemical treatments to address several issues at once.
“In the past, a customer might have been concerned primarily about corrosion or scale,” he recalls. “Today, in addition to minimizing corrosion and scale, they also may want to address iron, paraffin or other issues. In response, we are developing more combination products that solve three or four problems simultaneously rather than focusing on one or two.
“These products are more complex to create because we have to account for interactions between their components,” Disney notes. “However, the benefits can be significant. For example, producers often get better fluid separation and higher-quality fluids, which can translate to more efficient disposal.”
Long-Lasting Treatments
Even before supply chain disruptions increased triazine’s cost, there were strong reasons to consider other scavengers, assesses Deanna Callahan, technical engineering manager at Tall City Exploration III, a Permian Basin operator. “Triazine is relatively inexpensive and readily available, but it can pose environmental, health and safety risks. Triazine and its byproducts can be corrosive, so when we use it, we have procedures and equipment in place to keep people, facilities and the environment safe.
“Triazine is short-lived and needs to be continuously applied,” she adds. “Some of the new chemistries are able to scavenge more completely and remain active longer. On top of being safer for the environment and less damaging to casing, they can be more effective.”
To increase their longevity, both new chemistries and traditional staples can be encapsulated in a coating that gradually releases the chemistry. Callahan says Tall City is working with LFS Chemistry to test a coating that only releases the chemistries in the presence of H2S rather than responding to temperature or pH.
“When H2S encounters and activates the coating, the scavenger inside is released,” Callahan relates. “In a well without much H2S, the gradual release can be more affordable than continuously injecting triazine and investing in the associated equipment because the treatments only need to be pumped periodically. In wells that are heavily impacted by H2S, the downhole capsules protect the casing and keep production clean while an effective remediation strategy is developed and executed.”
To guide potential remediation efforts, Callahan says the capsules pumped down hole can contain tracers as well as scavengers. “If the capsules encounter H2S, they release their tracers alongside the scavenger,” he explains. “In a typical well, up to 10 tracers may be used. They can tell us whether H2S is coming from the lateral’s toe, one of the middle sections or the heel.
“If the toe is the source, a plug can be placed in the toe or a squeeze can be performed over the perforations there. If the source is toward the heel, which tends to be more productive, and a squeeze is unlikely to work, an expandable liner can be deployed to reduce H2S entry,” Callahan adds. “H2S travels, so the liner needs to be sized with a buffer around the problematic zone.”
Because these solutions block production, determining the issue’s source and isolating that area can have a huge impact on the well’s long-term economics. Without the ability to identify where H2S is entering the well, Callahan says, teams need to estimate where the H2S originated using imprecise indicators, such as how the well was fractured and when the H2S first appeared. “With the tracer aspect of this chemistry, we have a much clearer idea where the H2S comes from, which can be the difference between blocking off 800 feet of lateral production and 3,000,” she says.
Proactive Prevention
Callahan acknowledges that the encapsulated chemistry may cost more upfront. “However, it is significantly less expensive than over-remediating a well, so it is usually worthwhile,” she says.
“In general, Tall City tries to address issues while they still are easy to control rather than waiting for them to become economic pain points,” Callahan explains. “For example, we often build production facilities with equipment that can test the gas and administer treatments if specific problems develop. We may not need those capabilities on every well, but they are already in place if we do.”
As automation advances and chemical suppliers develop longer-lasting products, Callahan says many operators are moving toward earlier treatment and prevention. “We seek more knowledge of our wells before drilling and production,” she illustrates. “For example, we look at cuttings to evaluate the rock composition so we can predict where scale is likely to develop and potentially change the completion chemistry to prevent that.”
Callahan points out that she has discovered several alternatives to triazine through LinkedIn. “I also have gotten great ideas from conferences,” she reports. “The large conferences are valuable, but I also try to make time for smaller venues with more intimate settings where it’s easier to get into detailed conversations about specific products.”
According to Callahan, one of the keys to unlocking networking’s benefits is looking beyond fit-for-purpose solutions. “If I am only willing to learn about technologies that are already tailored to specific challenges, I miss out on tools I can adapt to my projects,” she says. “It takes time, but I try to learn what people are doing even if they face different problems or come from another industry.”
Precise Chemical Placement
Operators invest considerable time, effort and capital in selecting and designing the right artificial lift system for each of their wells. A capillary string (or CT line) is an economic way to ensure optimal lift system performance and extend run life while preserving the tubing string, according to Grant W. Galbraith, business development manager for capillary and gauges at PCS Ferguson, a business unit of ChampionX Artificial Lift.
“To maximize value, the artificial lift provider and capillary vendor need to be involved early in the design of the well, regardless of the type of lift method used,” he says.
Capillary strings are installed either by banding to the outside of production tubing or deploying it concentrically inside the tubing while the well is live. The technology is applicable to all forms of lift, providing a simple and proven concept for delivering continuous chemical to precisely the area of need, Galbraith relates.
“A large majority of oil and gas operators rely heavily on capillary systems as a cost-effective chemical delivery solution. In fact, capillary strings are used in most electric submersible pump deployments and a high percentage of gas lift wells,” he points out. “In a well with an ESP, the capillary string extends below to the pump intake depth. In a gas lift well, it delivers chemical to the end of the production tubing.”
Galbraith says wells with significant casing gas or fluid levels can create challenges when treating with delivery methods such as slip-streaming chemicals from the surface and down the backside of the casing. “These applications can make it more difficult to effectively treat with the recommended parts per million dosage of chemical. With a capillary string, every drop pumped at surface gets to where the well needs it the most,” he reports.
Moreover, Galbraith indicates that a properly designed, installed and maintained capillary system can be used for the entire life cycle of the well as it transitions from one type of lift to another–whether ESP, gas lift, rod pump, etc. “Capillary strings can be welded to add length and are extremely durable, enabling them to be pulled and reinstalled multiple times,” he says.
Best Capillary Practices
Although the concept behind a capillary injection system is straightforward, Galbraith emphasizes the need for proper design and installation, as well as awareness of yearly maintenance requirements. “It only takes one damaged or plugged string to turn a customer off the concept, so it is vital to follow best practices,” he cautions. “At the design stage, produced fluid and gas analysis, such as chloride content and partial pressures of carbon dioxide and H2S, should be reviewed to select the proper alloy.”
Installing capillary injection strings can increase artificial lift equipment’s runtime and performance by ensuring corrosion inhibitors and other chemistries get down hole in the recommended dosage. Noting that the strings can protect equipment throughout a well’s life, ChampionX says they deliver a strong return on investment as long as they are properly designed, maintained and deployed.
The most common CT line alloy is Super Duplex® 2205, but he notes that harsher environments may require Incoloy® 825 or Inconel® 625. The well’s artificial lift design and the way production will flow influence where the capillary string should be placed, so reviewing the artificial lift system early on is critical to achieving optimal performance, Galbraith advises.
“It’s also important for the operator to discuss with the chemical vendor whether products are tested and designated ‘capillary friendly.’ I have learned from our ChampionX chemical group that extensive lab time and simulation testing goes into designating products as fit-for-use in a capillary environment,” he states.
To mitigate the chance a string will be damaged during installation, Galbraith recommends operators communicate with their capillary provider regarding best practices and review standard operating procedures to understand and minimize risk.
“Take ownership of the job and communicate,” he offers. “Our spooling trailers are equipped with high-pressure capillary pumps, which are utilized to monitor the CT line. This allows the installers to notice any increase in pump pressure and verify the integrity of the capillary string during installation.”
He adds that follow-up maintenance is essential to getting a strong return on investment from the string. The maintenance includes periodically conducting a quick on-site process that involves a high-pressure flush and pressure test of the capillary string with reverse osmosis water or methanol. “The chemical filter manifolds should also be designed properly and cleaned regularly,” Galbraith continues. “We have created a manifold with added safety features. It’s been popular with our new installations.”
Galbraith says many of ChampionX Artificial Lift’s capillary injection string customers also are installing downhole pressure and temperature gauge systems with tubing encapsulated cable (TEC). A TEC system uses a 0.25-inch outside diameter tube with a 316 or 825 alloy outer shell. The inner core is a poly filler with 16- or 18-gauge wire.
Like capillary strings, TEC systems can be banded to production tubing or installed concentrically inside it, Galbraith notes. “The downhole gauge delivers continuous real-time pressure and temperature data, providing a valuable tool for monitoring offset fracs and well spacing or evaluating lift methods,” Galbraith concludes. “Our customers have definitely become ‘hooked on data.’ They see the value in the TEC and associated services, and continue requesting more systems to be installed.”
Sustainable Solvents
Terpenes can help the oil and gas industry provide much-needed energy to the world in an economic and sustainable way, says Trudy Boudreaux, vice president of product line management for Flotek Industries Inc. “These biodegradable molecules can increase production in both mature reservoirs with high gas-to-oil ratios, as well as mid- to low-GOR reservoirs containing less mature liquid hydrocarbons, paraffin and sometimes asphaltenes,” she reports.
In lab tests and the field, terpene-based solvents have proven effective at increasing production from oil and gas wells, Flotek Industries Inc. reports. Noting that they biodegrade and come from trees, fruits and plants, the company describes the terpenes as sustainable.
Terpenes are small, organic molecules found in various trees, fruits and plants. According to Boudreaux, they are excellent oil solvents. When blended with water, alcohol and surfactants to create microemulsions, the terpene solvents form nanoscopic droplets that are delivered to the reservoir surfaces, the liquid/liquid interfaces and the gas/liquid interfaces to improve reservoir connectivity, she relates.
“As a well is produced, hydrocarbons can deposit on the reservoir surface and restrict the aperture of the flow pathway. This can happen at the pore throat, along the flow network and near the wellbore,” Boudreaux notes. “Terpenes can expand the flow pathway’s aperture, which improves and extends reservoir productivity.”
In high GOR reservoirs, she continues, terpenes improve production primarily by addressing surface forces. In these applications, water is in contact with the dominantly gas phase within the reservoir. The lower the surface tension between the water and gas phase, the lower the pressure threshold needed for the hydrocarbon to push through the water phase, Boudreaux says. “Surfactants can lower the surface tension between the two phases, but we can achieve even greater reductions by pairing surfactants with terpenes,” she reports.
To see how much terpenes augment surfactants’ efficacy, Boudreaux recommends conducting laboratory tests in an enclosed environment. “Traditional methods of measuring surface tension, such as the Wilhelmy plate, do not allow terpenes’ effects to be measured because the system is open to the atmosphere. The terpene molecules migrate into the gas phase as expected but then escape, preventing their role from being observed,” she explains.
“When we perform tests in enclosed environments that more closely resemble the reservoir, terpenes’ benefits are easy to see,” Boudreaux says. “These lab results fit with production increases seen in the field.”
In both high- and low-GOR reservoirs, Boudreaux says terpenes work with surfactants to affect three production drivers: surface forces, wettability and the radius of the flow pathways.
“The wettability of the reservoir surface can enhance or restrict the ease with which fluids move through the reservoir,” Boudreaux suggests. “By including microemulsions in the completion fluid that create a neutral wettability, we can allow both aqueous and hydrocarbon phases to pass more readily through the reservoir network, increasing overall productivity.”
In low GOR reservoirs, terpenes help boost production across all stages of the well life cycle, from initial stimulation and production to remediation and tertiary recovery, she mentions. During initial completions, the terpenes are delivered through the aqueous phase in the form of microemulsions. During the remediation phase, they frequently are mixed with surfactants or deployed as undiluted solvent treatments, with the approach depending on reservoir conditions.
“As biodegradable solvents, terpenes are a win for production and the environment,” Boudreaux states. “They have long been associated with the citrus market, particularly the large volume of oranges consumed globally, but in the 20 years since Flotek began working with terpenes, we have acquired them from a variety of plant-based sources. This flexibility helps us build efficient and resilient supply chains that shrink energy production’s environmental impacts on air, water, land and people.”
Increasing Production
Between 2010 and 2020, more than 90,000 wells were drilled in major U.S. unconventional plays, says Michael Lantz, co-founder and chief executive officer of Kairos Energy Services LLC.
By using diverters to distribute chemistries throughout the lateral, Kairos Energy Services reports it can boost mature unconventional wells’ production and remediate damage, including water block from frac hits. In the Eagle Ford, the company’s process has yielded substantial increases in production and reserves.
“My partners and I formed Kairos with the goal of developing a low-cost, low-risk treatment to improve production from these mature unconventional wells,” he recounts. “The solution we came up with can increase production 30%-60% and add 10%-20% to reserves while paying for itself within six months.”
The company’s process involves pumping chemicals down hole to enhance hydrocarbon flow and remediate damage, Lantz outlines. “The chemistries we use vary from well to well, but they often include surfactants to reduce interfacial tension and address water block, which is common in older unconventional wells or ones that have experienced a frac hit. We also can remediate scaling, paraffin deposits or gummy bear issues from cross-linked gels.”
To distribute the treatment across the lateral and into the various fractures, Lantz says Kairos deploys biodegradable particulate diverters in a special fluid. “These diverters block against the proppant, so we vary the particle size distribution based on the perforations’ characteristics and the size of the proppant,” he says. “By analyzing pressure responses and pump charts from field trials, we know the diverters work.”
Instead of dissolving in downhole fluids, the diverters degrade in response to temperature, an approach Lantz describes as more reliable. He says they usually turn into a liquid 24-48 hours after deployment.
“Our process is low risk,” he assures. “Most wells we treat will not require any mechanical intervention. All we need are two or three frac pumps, a blender and some frac tanks full of water. We can take care of the rest.”
Pumping the treatments takes anywhere from 12 to 24 hours, after which Lantz recommends shutting in the well for two days. “Three days of downtime is a small trade-off to get 20% more production from a well,” he assesses.
Broad Appeal
According to Lantz, many wells can benefit from Kairos Energy Services’ treatments. “For mature unconventional wells, we focus on ones performing below expectations,” he says. “We analyze those wells to look for signs of specific problems, such as changes in the rate transient analysis indicating damage, unusually high water cuts or rapid changes in the gas-to-oil ratio, all of which can indicate water block or other addressable damage.”
The company often treats newer wells to remediate frac hits, Lantz reports. Alternately, it can help prevent a hit by filling a well with fluid to keep it from acting as a pressure sink. “Our diverters can distribute fluid effectively across the whole lateral and build more pressure for each barrel of water injected,” Lantz says. “We often see 50% more pressure than comparable wells that have been prefilled without diverters.”
Lantz adds that the frac hit protection fluids contain production-enhancing chemistries. Noting that the company’s first deployment took place in November 2020, he says Kairos has worked in the Eagle Ford, Denver-Julesburg, Bakken and Powder River plays. “We are excited about what we have been able to achieve,” he comments. “This year, we will be scaling up to a commercial level with our first client in the Eagle Ford and potentially conducting trials in the Permian and SCOOP/STACK.”
Automation’s Benefits
Automating chemical injection pumps can yield significant returns, says Chad Hammond, president of DCiii Control. “When we use our control system to automatically adjust the injection rate as fluid volumes change, we typically see a 10%-30% optimization in chemical volumes,” he reports. “This often means reducing chemical consumption, but sometimes we end up increasing it to avoid underdosing, which can lead to expensive issues.”
Hammond says optimizing treatment volumes is especially important today, when supply chain disruptions have made it difficult and increasingly expensive to source many chemicals.
By pairing a robust sight glass with a power-efficient controller, DCiii Control says it can automate almost any chemical injection pump. The company’s system maintains the desired dosage while giving users real-time visibility into chemical consumption and pump behavior.
“Our automation system can pay for itself rapidly,” he suggests. “For particularly troubled injection points or ones where volumes fluctuate frequently, payback can be as fast as a few days or a week. For new wells, it usually takes a month or two. For wells between six months and five years old, or other injection points, the equipment often pays for itself in two-six months.”
DCiii’s equipment replicates the steps chemical technicians or pumpers normally take if they manage sites manually. “When technicians get to a site, they walk up to the chemical tank, isolate a sight glass off to the side and watch the pump run to figure out how quickly it’s injecting. Then they adjust the pump to match the prescribed injection rate, which is often written on a clipboard,” Hammond describes.
“With our system, we can repeat the same steps every five-15 minutes,” he says. “This changes technicians’ job from driving around to check every injection point for which they’re responsible, which can be anywhere from 50 to 400, to managing by exception. They get a report in the morning that identifies injection points with abnormal behavior, and only need to drive to those. In addition to saving time and money, this reduces driving-related safety risks and emissions.”
Enabling Automation
Building equipment to automate chemical injection is quite a challenge, Hammond reflects. “When my father and I first began to look at automating chemical injection in 2015, we planned to be a distributor, but we could not find any equipment we felt comfortable putting our name on,” he recalls. “Instead, we launched DCiii and spent the next three years developing hardware and software that would work.”
The company quickly decided that rather than trying to reinvent the wheel, it would use the same sight-glass-based process technicians had proven across several decades. To do that, the company uses two components: a sight glass and a controller. “Because the glass hangs off the chemical tank, it needs to be light and short,” Hammond notes. “To minimize failure points, it only has one moving part, an actuator that is rated for 15 million cycles, enough to last more than 15 years.”
To assess the pump’s speed, Hammond says the system periodically closes the valve to isolate the sight glass and pump from the tank, then uses a hydrostatic pressure sensor to see how quickly the pump draws chemical from the sight glass. This speed helps the controller decide how to achieve the desired injection rate.
According to Hammond, designing the controller took care. “Many injection points are in remote areas where the only power comes from a solar panel that was installed primarily to run the injection pump and may be undersized even for that, so minimizing power consumption was extremely important,” he says. “Even a tiny PLC will draw too much power and require too much wiring, so our engineering team has created a low-power circuit board and telemetry system.”
This controller is sophisticated enough to monitor and interpret the pump’s condition and respond appropriately, Hammond assures. As an example, he says it can compensate for variations in voltage on cloudy days in which the pump gets inadequate power.
DCiii’s system can target a prescribed injection rate or turn the pump on and off at user-defined intervals, Hammond says, but many customers prefer to have it change the injection rate in proportion to fluid volumes. This setting lets the system maintain an effective chemical concentration, such as 60 parts per million, as production fluctuates.
The data the system collects gives both operators and chemical service providers real-time visibility into the field and a record of what has happened at a particular injection point, Hammond adds, noting this information can guide optimization efforts.
“The system works with almost any supervisory control and data acquisition setup and is completely agnostic to the pump, the tank or the type of chemical,” Hammond says. “As of early February, we have 3,000 systems in the field. Three-fourths are managing corrosion or scale inhibitors, but we have quite a few injecting methanol, H2S scavengers and other types of chemicals.”
For other great articles about exploration, drilling, completions and production, subscribe to The American Oil & Gas Reporter and bookmark www.aogr.com.