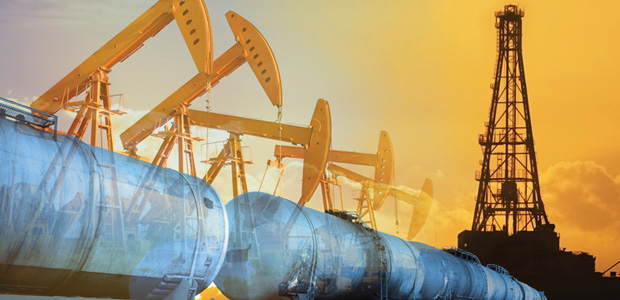
Production Automation
Wireless Sensors Help Optimize Pads
By Jim Gardner
FOOTHILL RANCH, CA.–Oil and natural gas producers are learning to deal with new operational paradigms in which optimizing producing assets to maintain production is the mantra of the day. However, that is a challenging undertaking in tight oil and gas shale plays, given the scope of field developments as well as first-year productivity decline curves as high as 80 percent.
In plays such as the Bakken, Permian and Eagle Ford, a typical pad can have 10 or more horizontal wells with significant production equipment on site. These pads typically have nearby centralized facilities sized to handle the high initial production volumes, along with all of the associated equipment and gathering systems. Producers operating multiple pads at various stages on the decline curve (and perhaps using various forms of artificial lift technologies) are relying on technology to better manage this highly dynamic production environment and improve bottom-line performance and reserves recovery.
It does not take a doctorate in economics to understand why optimizing existing wells has become a critical factor in successfully managing unconventional assets. With the new production dynamics, the age of “big data” has come to the forefront. Optimization requires a constant stream of data on pressure, temperature and flow levels. The data must be accurate, timely and economically attainable. The formula for business success for shale operators can be expressed as “data = analytics = better decision making.”
Data impact business decisions and build business intelligence to allow operating companies to better manage asset performance. The key objectives for data analytics and automation solutions are to enhance production, streamline operations, eliminate downtime, and boost recoveries. Critical information for this new cycle includes data to assess what happened in the event of well stoppage or production loss. This can be as simple as having a stock tank filled to capacity, or as problematic as having tubing pressure drop dramatically in seconds.
From that point, the issue becomes understanding exactly why a problem happened. By having near-real-time data and applying that data to trend charts and other analytical tools, engineers can investigate the time leading to a change in operating conditions to understand the “why” behind a production issue or equipment failure.
The next, and arguably most critical, step is the ability to learn, predict and forecast what is likely to happen in the future to institute changes designed to prevent unscheduled production interruptions and allow wells/pads to produce at their optimum capacities.
Optimizing Performance
Given all the production variables and equipment involved, it is easy to understand how producers with multiple pads can become overwhelmed with trying to manage all the pads, let alone figuring out how to optimize each individual well’s performance. Many of the decisions fundamental to optimizing well performance must be made on location by intelligent automation devices such as programmable logic controllers (PLCs) or remote terminal units. To accomplish this, the remote sensors must be placed wherever critical operational data are required, such as tank levels, flowmeters, casing and tubing pressures, chemical injection, sand filtration, pumps and separators, compressors, flare stack monitors, etc.
The equipment on a production site in conventional fields may have included one wellhead, three storage tanks, and separator. In unconventional resource plays with multiple wellheads on each site, production facilities have become much larger as well as much more elaborate. In fact, 40 or more sensors may be required to acquire all the data necessary to optimize production.
Low-cost wireless sensors acquire accurate real-time data on critical processes and equipment to enable better decision making for optimizing the performance of multiwell pads, improving personnel safety, and ensuring regulatory compliance in unconventional resource plays.
The expanded scope of operations and equipment on pad sites has grown exponentially the cost of equipping and installing locations with sensors, automation controls and communications devices. The cost of conduit, trenching and labor for oil and water storage tanks alone can exceed $2,000 a tank. Extrapolating that to a 24-tank battery equates to $48,000 for installation, not counting the equipment that will be required to acquire and communicate data for monitoring the tank battery. In a fully wired, fully instrumented production facility, the required automation can cost $250,000 a site.
As multiwell pads have become the norm in shale production, the industry has shifted increasingly from conventional wired communications to wireless solutions for remote sensor and automation components. In some cases, operators may find it advantageous to combine technologies to complete hybrid solutions that combine layers of communications, such as Ethernet, serial and wireless. But one of the key driving factors behind wireless technology’s adoption is the fact that it costs 30 percent less on average than wired solutions. In addition, wireless equipment is portable, allowing it to be moved on or off location at almost no cost.
Critical Considerations
With production companies seeking to maintain and optimize production, both the cost and efficiency of the remote sensing equipment used to automate operations are becoming critical considerations. Automation in the oil and gas industry started as a way to report gas flows and tank fluid levels, with early automation systems providing “report only” functionality. Today, integrated automation systems include monitoring, reporting, control and built-in fail safe capabilities.
Most automated production facilities rely on automated emergency shut down (ESD) systems, cry-out-by-exception alarms, and much smarter and more memory-intensive intelligent devices such as PLCs and RTUs. The purpose of incorporating wired or wireless automation into oil and gas operations is to enhance bottom-line economics by increasing life cycle productivity, reducing installation costs, improving quality or the predictability of quality, improving the robustness of production processes, reducing human labor and intervention, and mitigating safety and environmental risks.
Similar to the evolution of wired to wireless control systems, capital cost and operating expense are dominant factors in the development of automation technology, but almost equally important is the time to implement data analysis. Reducing wait times from weeks to days or hours means operators can receive data sooner, and start to plot trends and cycles earlier in the production process to analyze performance and optimize production from the first day a well comes on line. Having accurate, timely information that can be implemented quickly and economically allows operators to take pre-emptive steps to identify issues, prevent problems and enhance production operations.
These new operational capabilities reflect the evolving concepts of big data and the fully digital oil field. It is estimated that 50 percent of all oil and gas production companies will have the ability to perform predictive analysis within the next year. Already, the industry has migrated from 100 percent wired solutions to the point where 50 percent of all supervisory control and data acquisition system installations use wireless technology, and the trend to wireless solutions continues to accelerate rapidly.
Custody Transfer
The well pad and the associated production facilities represent the first and primary focal point in the process of optimizing field operations. The second point is custody transfer, where remote sensors and data acquisition have become equally critical. The challenges in custody transfer operations break into four separate, but related issues: preventing spills, preventing theft, reporting accurate inventory levels, and accurately measuring sales volumes.
The challenges are complicated because changes in production rates from pads in unconventional plays can cause operators to have insufficient or excess separation and tank storage, inefficient compression, and other capacity issues on wells that could be better utilized on other pads. With the advent of multiwell pads, production locations have more or less become processing plants. Large volumes of oil and gas are being produced, treated, stored and transferred. As the product moves away from the pad location, the challenge shifts from optimizing production to optimizing the accountability and accuracy of the sales.
In U.S. unconventional resource plays, leading producers such as Apache, Pioneer Natural Resources, BHP Billiton, Anadarko, Statoil and Range Resources have led the way with information technology-driven data solutions. Smaller companies traditionally have been slower to adopt automation and optimization technologies, but that trend clearly has reversed. Smaller operators are installing remote sensors on well and pad locations to allow them to better analyze production data today, as well as to implement predictive analysis and optimization efforts in the future.
HS&E Issues
An additional critical driver in the industry’s move to digital oil field technology is health, safety and environmental compliance. In areas where hydrogen sulfide is an operational hazard, most companies have enacted policies to prohibit employees or contractors from hand gauging tanks or even going up the stairs to the “catwalk” on storage tanks.
Installing sensors on these sites introduces risk and requires crews to be trained and certified in H2S safety. Many producers are seeking to protect their employees and mitigate operational risk by adopting wireless technologies that can be installed fully in 30 minutes per tank by one man as opposed to two days for a two- to three-man crew. The less time spent in a hazardous environment means the less time that employees and contractors are exposed to risk.
Ever-stricter federal and state regulations on allowable emissions from production locations also are speeding the adoption of wireless sensor solutions. In Colorado, for example, detectable emissions from an open thief hatch on a storage tank can incur a fine of $15,000 per tank per day. To assure compliance with local and federal regulations, operators are looking for accurate, near-real-time alarm systems. For producers with large numbers of tanks to monitor, the cost and reliability of alarm systems in challenging oil field environments are paramount. The low cost, deployment speed and dependable performance of wireless technology make it well suited for these applications.
Without timely and accurate information, producers cannot monitor assets reliably, identify trends or improve performance. Data analytics provide oil and gas companies with the opportunity to optimize production from the level of an individual well, to a multiple-well pad, to multiple pads spread across an entire development area. While there certainly are obstacles to overcome, wireless sensing equipment continues to evolve rapidly, with production and midstream companies paving the way to innovative applications for automating and optimizing assets.
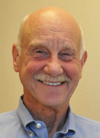
Jim Gardner is a regional vice president at OleumTech Corporation. He has worked in the oil and gas industry since 1975. Before joining the company, Gardner served for 12 years as oil and gas industry manager at FreeWave Technologies Inc. Prior to that, he had served as a regional manager at AMF Tuboscope, senior vice president and general manager at Remote Operating Systems, and product manager at ABB Totalflow. Gardner holds a bachelor’s from the University of Washington.
For other great articles about exploration, drilling, completions and production, subscribe to The American Oil & Gas Reporter and bookmark www.aogr.com.